Catalyst as well as preparation and application thereof
A technology of catalysts and additives, applied in physical/chemical process catalysts, chemical instruments and methods, ammonia-carboxylic acid reaction preparation, etc. Long, selective and active effect
- Summary
- Abstract
- Description
- Claims
- Application Information
AI Technical Summary
Problems solved by technology
Method used
Examples
Embodiment 1
[0036] Pseudoboehmite (Al 2 o 3 Add 300.0g of 300.0g in batches (15g per batch, interval of 2-3min) to 471.2g of concentrated phosphoric acid (concentration: 85.54%) uniformly stirred at 50°C, dry to constant weight after addition, and grind , sieved. Add 18.4g of turnip powder, 3.1g of hydroxymethyl cellulose, 12.3g of nitric acid (concentration 15wt%), and 110.4g of deionized water into the above-mentioned sieved powder, knead and extrude into φ3 (3-5mm ) clover-shaped catalyst particles, dried to constant weight. Put it into a muffle furnace, raise the temperature to 300°C at a heating rate of 2.5°C / min, keep it for 2 hours, and then raise the temperature to 600°C for 4 hours. Put the calcined catalyst in a quartz tube, put it into a tubular heating furnace, set the temperature at 450°C, and after reaching the temperature, follow the 1.0h -1 Pump in deionized water at a certain space velocity, treat for 4 hours, take it out and dry it to constant weight to obtain the ca...
Embodiment 2
[0038] Add 1.5kg of aluminum nitrate nonahydrate in batches (50g per batch, interval of 2-3min) into 471.2g of concentrated phosphoric acid (concentration: 85.54%) uniformly stirred at 50°C, dry to constant weight after addition, and grind , sieved. Add 18.4g of turnip powder, 12.3g of nitric acid (concentration 15wt%), and 110.4g of deionized water into the above-mentioned sieved powder, knead and extrude into clover-shaped catalyst particles of φ3 (3-5mm), and dry to constant weight. Put it into a muffle furnace, raise the temperature to 300°C at a heating rate of 2.5°C / min, keep it for 2 hours, and then raise the temperature to 600°C for 4 hours. Put the calcined catalyst in a quartz tube, put it into a tubular heating furnace, set the temperature at 450°C, and after reaching the temperature, follow the 1.0h -1 Pump in deionized water at a certain space velocity, treat for 4 hours, take it out and dry it to constant weight to obtain the catalyst.
Embodiment 3
[0040]Add 321.2g of aluminum hydroxide powder in batches (16g per batch, interval of 2-3min) into 471.2g of concentrated phosphoric acid (concentration: 85.54%) uniformly stirred at 50°C, dry to constant weight after addition, and grind , sieved. Add 18.4g of turnip powder, 12.3g of nitric acid (concentration 15wt%), and 110.4g of deionized water into the above-mentioned sieved powder, knead and extrude into clover-shaped catalyst particles of φ3 (3-5mm), and dry to constant weight. Put it into a muffle furnace, raise the temperature to 300°C at a heating rate of 2.5°C / min, keep it for 2 hours, and then raise the temperature to 600°C for 4 hours. Put the calcined catalyst in a quartz tube, put it into a tubular heating furnace, set the temperature at 450°C, and after reaching the temperature, follow the 1.0h -1 Pump in deionized water at a certain space velocity, treat for 4 hours, take it out and dry it to constant weight to obtain the catalyst.
PUM
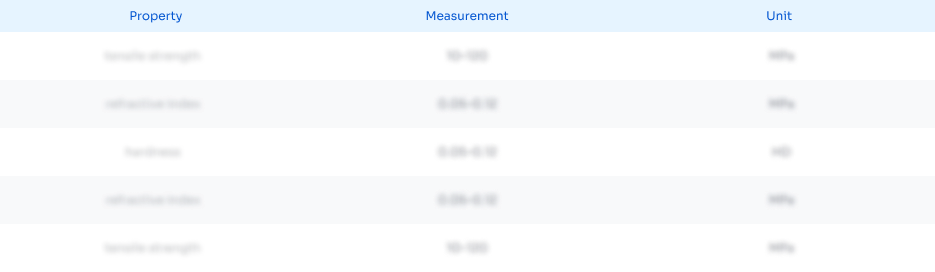
Abstract
Description
Claims
Application Information

- Generate Ideas
- Intellectual Property
- Life Sciences
- Materials
- Tech Scout
- Unparalleled Data Quality
- Higher Quality Content
- 60% Fewer Hallucinations
Browse by: Latest US Patents, China's latest patents, Technical Efficacy Thesaurus, Application Domain, Technology Topic, Popular Technical Reports.
© 2025 PatSnap. All rights reserved.Legal|Privacy policy|Modern Slavery Act Transparency Statement|Sitemap|About US| Contact US: help@patsnap.com