Method and device for growth ofnitride materials at low temperature through laser assistance
A laser-assisted, nitride technology, applied in metal material coating process, gaseous chemical plating, coating and other directions, can solve the problem of the reduction of nitride film growth quality and efficiency, difficulty in mass production and commercialization, substrate The problem of high material cost, to achieve the effect of improving quality, improving growth rate and quality, and improving quality and performance
- Summary
- Abstract
- Description
- Claims
- Application Information
AI Technical Summary
Problems solved by technology
Method used
Image
Examples
example 1
[0071] Taking the growth of gallium nitride film layer material on a sapphire (other substrate materials are also applicable) substrate as an example, the specific operation steps of this embodiment are as follows:
[0072] (1) Preparatory work: the substrate material 12 is placed on the upper surface of the heater 13, and the reaction chamber 4 is pumped into 10 with a vacuum pump. -2 Vacuum state below Torr;
[0073] (2) Start the heater to heat the substrate to 600°C;
[0074] (3) Nitrogen gas is used as the carrier gas to transport the liquid vapor of the precursor TMGa 5 into the reaction chamber as a gallium source for nitride deposition; ammonia gas 6 is used as a nitrogen source for nitride deposition. The two enter the gas pre-mixing chamber 9 through the carrier gas inlet pipe 7 and the nitrogen source inlet pipe 8 respectively for mixing. Among them, TMGa is evaporated from a liquid, and can only use an inert gas (such as nitrogen) as a carrier. Adjust the gas fl...
example 2
[0083] Taking the growth of gallium nitride film layer material on a sapphire (other substrate materials are also applicable) substrate as an example, the specific operation steps of this embodiment are as follows:
[0084] (1) Preparatory work: the substrate material 12 is placed on the upper surface of the heater 13, and the reaction chamber 4 is pumped into 10 with a vacuum pump. -2 Vacuum below Torr;
[0085] (2) Start the heater to heat the substrate to 500°C;
[0086] (3) Nitrogen gas is used as the carrier gas to transport the liquid vapor of the precursor TMGa 5 into the reaction chamber as a Ga source for nitride deposition; ammonia gas 6 is used as a nitrogen source for nitride deposition. The two enter the gas pre-mixing chamber 9 through the carrier gas inlet pipe 7 and the nitrogen source inlet pipe 8 respectively for mixing. Among them, TMGa is evaporated from a liquid, and can only use inert gas (such as nitrogen) as a carrier. The ratio of TMGa steam to nitr...
example 3
[0092] Taking the growth of gallium nitride film layer material on a single crystal silicon substrate as an example, the specific operation steps of this embodiment are as follows:
[0093] (1) Preparatory work: the substrate material 12 is placed on the upper surface of the heater 13, and the reaction chamber 4 is pumped into 10 with a vacuum pump. -2 Vacuum below Torr;
[0094] (2) Start the heater to heat the substrate to 600°C;
[0095] (3) Nitrogen gas is used as the carrier gas to transport the liquid vapor of the precursor TMGa 5 into the reaction chamber as a Ga source for nitride deposition; ammonia gas 6 is used as a nitrogen source for nitride deposition. The two enter the gas pre-mixing chamber 9 through the carrier gas inlet pipe 7 and the nitrogen source inlet pipe 8 respectively for mixing. Among them, TMGa is evaporated from a liquid, and can only use inert gas (such as nitrogen) as a carrier. The ratio of TMGa steam to nitrogen is 1:50; the ratio of ammonia...
PUM
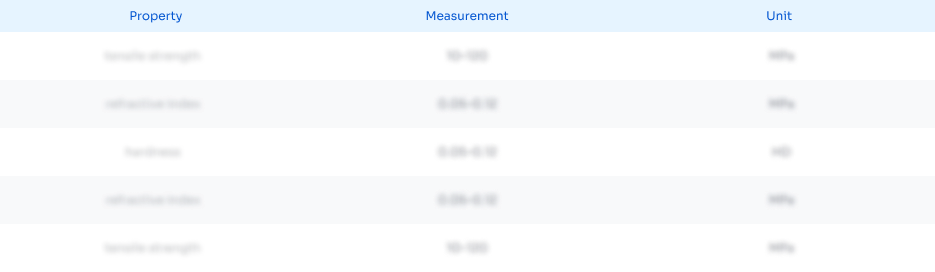
Abstract
Description
Claims
Application Information

- R&D Engineer
- R&D Manager
- IP Professional
- Industry Leading Data Capabilities
- Powerful AI technology
- Patent DNA Extraction
Browse by: Latest US Patents, China's latest patents, Technical Efficacy Thesaurus, Application Domain, Technology Topic, Popular Technical Reports.
© 2024 PatSnap. All rights reserved.Legal|Privacy policy|Modern Slavery Act Transparency Statement|Sitemap|About US| Contact US: help@patsnap.com