Composite kraft paper manufacturing process
A manufacturing process and technology of kraft paper, applied in papermaking, papermaking, textiles and papermaking, etc., can solve the problems of unfavorable use, high production cost, difficult to treat wastewater, etc., and achieve the effect of fine surface layer, low cost and good whiteness
- Summary
- Abstract
- Description
- Claims
- Application Information
AI Technical Summary
Problems solved by technology
Method used
Examples
Embodiment 1
[0029] The manufacturing process of composite kraft paper, the composite kraft paper includes a surface layer and a bottom layer, and the surface layer and the bottom layer are closely bonded. The manufacturing process includes the following steps:
[0030] (1) Selection of raw materials: use bleached softwood pulp and hardwood pulp to prepare the surface layer slurry in a weight ratio of 1:1, and use semi-bleached waste paper pulp and bamboo wood pulp to mix in a weight ratio of 2:1 Prepare bottom slurry;
[0031] (2) Preparation of surface layer slurry: put softwood pulp and hardwood pulp into the pulping tank of the surface layer slurry according to the weight ratio of 1:1, and add industrial water into the pulping tank, stir and mix evenly, Obtain surface layer mixed slurry, the concentration of surface layer mixed slurry is 3.7%;
[0032] (3) Preparation of the bottom layer slurry: put waste paper pulp and bamboo wood pulp in the pulping tank of the bottom layer slurry a...
Embodiment 2
[0038] The manufacturing process of composite kraft paper, the composite kraft paper includes a surface layer and a bottom layer, and the surface layer and the bottom layer are closely bonded. The manufacturing process includes the following steps:
[0039] (1) Selection of raw materials: use bleached softwood pulp and hardwood pulp to prepare the surface layer slurry in a weight ratio of 1:1, and use semi-bleached waste paper pulp and bamboo wood pulp to mix in a weight ratio of 2.5:1 Prepare bottom slurry;
[0040] (2) Preparation of surface layer slurry: put softwood pulp and hardwood pulp into the pulping tank of the surface layer slurry according to the weight ratio of 1:1, and add industrial water into the pulping tank, stir and mix evenly, Obtain surface layer mixed slurry, the concentration of surface layer mixed slurry is 4.5%;
[0041] (3) Preparation of the bottom layer slurry: put waste paper pulp and bamboo wood pulp in the pulping tank of the bottom layer slurry...
Embodiment 3
[0047] The manufacturing process of composite kraft paper, the composite kraft paper includes a surface layer and a bottom layer, and the surface layer and the bottom layer are closely bonded. The manufacturing process includes the following steps:
[0048] (1) Selection of raw materials: use bleached softwood pulp and hardwood pulp to prepare the surface layer pulp in a weight ratio of 1:1, and use semi-bleached waste paper pulp and bamboo wood pulp to mix in a weight ratio of 3:1 Prepare bottom slurry;
[0049] (2) Preparation of surface layer slurry: put softwood pulp and hardwood pulp into the pulping tank of the surface layer slurry according to the weight ratio of 1:1, and add industrial water into the pulping tank, stir and mix evenly, Obtain surface layer mixed slurry, the concentration of surface layer mixed slurry is 5.2%;
[0050] (3) Preparation of the bottom layer slurry: put waste paper pulp and bamboo wood pulp in the pulping tank of the bottom layer slurry acc...
PUM
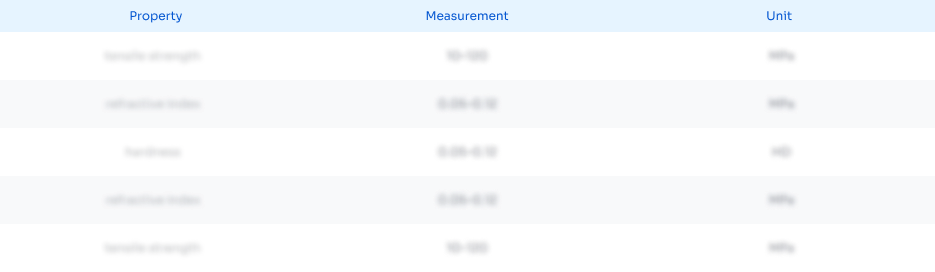
Abstract
Description
Claims
Application Information

- Generate Ideas
- Intellectual Property
- Life Sciences
- Materials
- Tech Scout
- Unparalleled Data Quality
- Higher Quality Content
- 60% Fewer Hallucinations
Browse by: Latest US Patents, China's latest patents, Technical Efficacy Thesaurus, Application Domain, Technology Topic, Popular Technical Reports.
© 2025 PatSnap. All rights reserved.Legal|Privacy policy|Modern Slavery Act Transparency Statement|Sitemap|About US| Contact US: help@patsnap.com