Preparation method of corrosion-resistant flame-retardant paint
A corrosion-resistant and paint-resistant technology, applied in the paint field, achieves the effects of few steps, mild reaction conditions, and simple and easy-to-operate preparation methods
- Summary
- Abstract
- Description
- Claims
- Application Information
AI Technical Summary
Problems solved by technology
Method used
Image
Examples
Embodiment 1
[0025] A method for preparing a corrosion-resistant and oil-resistant paint, comprising the following steps: (1) pretreatment: vacuum-drying the main resin at 100°C for 36h, removing water for later use; (2) heating 89g of the pretreated main resin to 50°C, adding 67g of monomer diluent, 1200r / min high-speed stirring for 60min; (3) heating up to 130°C, adding 10g of initiator, 17g of antistatic agent, 17g of flame retardant and 17g of matting agent, and reacting for 3.5h; (4) cooling down to 92 ℃, add 10g of antibacterial agent, 12g of ultraviolet absorber and 1g of defoamer, and react for 2.5h; (5) Slowly cool down to 45°C while stirring, ultrasonically disperse for 20min, and cool down to room temperature.
Embodiment 2
[0027] A method for preparing a corrosion-resistant and oil-resistant paint, comprising the following steps: (1) pretreatment: vacuum-drying the main resin at 100°C for 48h, removing water for later use; (2) heating 101g of the pretreated main resin to 60°C, adding 82g of monomer diluent, 2000r / min high-speed stirring for 90min; (3) heating up to 145°C, adding 15g of initiator, 29g of antistatic agent, 29g of flame retardant and 35g of matting agent, and reacting for 5.5h; (4) cooling down to 95 ℃, add 16g of antibacterial agent, 15g of ultraviolet absorber and 11g of defoamer, react for 3.5h; (5) Slowly cool down to 50℃ while stirring, ultrasonically disperse for 45min, then cool down to room temperature.
Embodiment 3
[0029] A method for preparing a corrosion-resistant and oil-resistant paint, comprising the following steps: (1) pretreatment: vacuum-drying the main resin at 100°C for 42 hours, removing water for later use; (2) heating 99g of the pretreated main resin to 55°C, adding 78g of monomer diluent, 1800r / min high-speed stirring for 80min; (3) heating up to 140°C, adding 13g of initiator, 19g of antistatic agent, 27g of flame retardant and 23g of matting agent, and reacting for 4h; (4) cooling down to 95°C , add 15g of antibacterial agent, 14g of ultraviolet absorber and 7g of defoamer, and react for 3h; (5) Slowly cool down to 45°C while stirring, ultrasonically disperse for 40min, and cool down to room temperature.
PUM
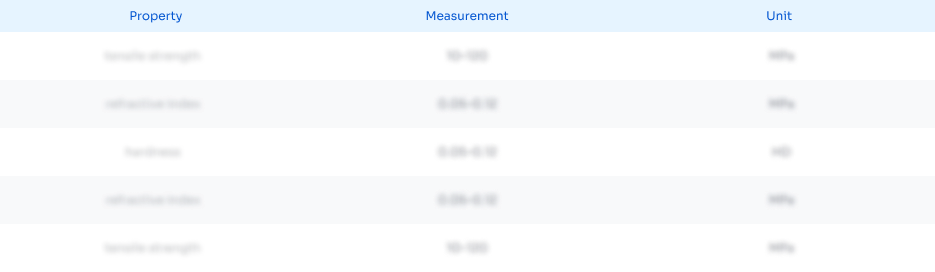
Abstract
Description
Claims
Application Information

- Generate Ideas
- Intellectual Property
- Life Sciences
- Materials
- Tech Scout
- Unparalleled Data Quality
- Higher Quality Content
- 60% Fewer Hallucinations
Browse by: Latest US Patents, China's latest patents, Technical Efficacy Thesaurus, Application Domain, Technology Topic, Popular Technical Reports.
© 2025 PatSnap. All rights reserved.Legal|Privacy policy|Modern Slavery Act Transparency Statement|Sitemap|About US| Contact US: help@patsnap.com