Method for constructing multistage ordered microstructure by combination of template imprinting and surface wrinkling
A combined, microstructured technology, applied in the direction of chemical instruments and methods, lamination, lamination devices, etc., to achieve the effect of wide application prospects, low technical cost, and wide application range
- Summary
- Abstract
- Description
- Claims
- Application Information
AI Technical Summary
Problems solved by technology
Method used
Image
Examples
Embodiment 1
[0022] A method for constructing a multi-level ordered microstructure by combining template imprinting and surface wrinkling, comprising the following steps:
[0023] (1) Fix the PDMS elastomer on the stretching table with a pre-stretch rate of 10% for preparing a wrinkle template; a stretch rate of 5% for transferring the PS film;
[0024] (2) The stretched PDMS used to prepare the wrinkle template is treated with oxygen plasma for 10 minutes, and the wrinkle template with a regular shape is obtained after retraction;
[0025] (3) In a water bath environment, transfer the spin-coated 2wt% PS film on the glass substrate to the stretched PDMS used to transfer the PS film in step (1) to form a PDMS / PS double-layer system, and dry it under vacuum ;
[0026] (4) Cover the wrinkle template prepared in step (2) on the PDMS / PS bilayer system that has been vacuum-dried in step (3) at an angle of 90 degrees to the PDMS stretching direction, and heat it at 90 degrees Celsius for 2 hour...
Embodiment 2
[0029] (1) Fix the PDMS elastomer on the stretching table, the pre-stretch rate is 5%, and it is used to prepare the wrinkle template; the stretch rate is 10%, and it is used to transfer the PS film;
[0030] (2) The stretched PDMS used to prepare the wrinkle template is treated with oxygen plasma for 10 minutes, and the wrinkle template with a regular shape is obtained after retraction;
[0031] (3) In a water bath environment, transfer the spin-coated 3wt% PS film on the glass substrate to the stretched PDMS used to transfer the PS film in step (1) to form a PDMS / PS double-layer system, and dry it under vacuum conditions ;
[0032] (4) Cover the wrinkle template prepared in step (2) on the PDMS / PS bilayer system that has been vacuum-dried in step (3) at an angle of 50 degrees to the PDMS stretching direction, and heat it at 105 degrees Celsius for 1 hour Cool to room temperature, remove the wrinkle template, and obtain the first-order morphology;
[0033] (5) The PDMS / PS / b...
Embodiment 3
[0035] (1) Fix the PDMS elastomer on the stretching table with a pre-stretch rate of 5%, which is used to prepare a wrinkle template; a stretch rate of 5%, which is used to transfer the PS film;
[0036] (2) The stretched PDMS used to prepare the wrinkle template was treated with oxygen plasma for 15 minutes, and a wrinkle template with a regular shape was obtained after retraction;
[0037] (3) In a water bath environment, transfer the spin-coated 2wt% PS film on the glass substrate to the stretched PDMS used to transfer the PS film in step (1) to form a PDMS / PS double-layer system, and dry it under vacuum ;
[0038] (4) Cover the wrinkle template prepared in step (2) on the PDMS / PS bilayer system that has been vacuum-dried in step (3) at an angle of 0 degrees to the PDMS stretching direction, and heat it at 120 degrees Celsius for 0.5 hours Cool to room temperature, remove the wrinkle template, and obtain the first-order morphology;
[0039] (5) The PDMS / PS / bilayer system ...
PUM
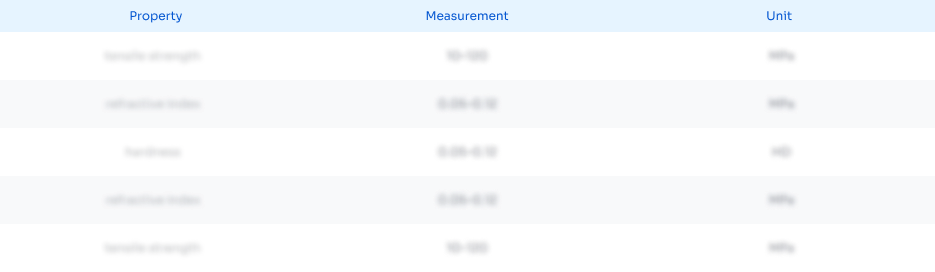
Abstract
Description
Claims
Application Information

- R&D
- Intellectual Property
- Life Sciences
- Materials
- Tech Scout
- Unparalleled Data Quality
- Higher Quality Content
- 60% Fewer Hallucinations
Browse by: Latest US Patents, China's latest patents, Technical Efficacy Thesaurus, Application Domain, Technology Topic, Popular Technical Reports.
© 2025 PatSnap. All rights reserved.Legal|Privacy policy|Modern Slavery Act Transparency Statement|Sitemap|About US| Contact US: help@patsnap.com