Aluminum alloy wheel punching method
An aluminum alloy and wheel technology, applied in metal processing equipment, metal processing machinery parts, manufacturing tools, etc., can solve the problems of affecting the processing accuracy of product performance, inability to ensure distribution, affecting processing efficiency, etc., to improve production efficiency and pass rate. , The effect of reducing the scrap rate of defective products and reducing production costs
- Summary
- Abstract
- Description
- Claims
- Application Information
AI Technical Summary
Problems solved by technology
Method used
Image
Examples
Embodiment Construction
[0029] The present invention will be further described in detail below in conjunction with the accompanying drawings and through specific embodiments. The following embodiments are only descriptive, not restrictive, and cannot limit the protection scope of the present invention.
[0030] A kind of aluminum alloy wheel punching process, concrete steps are as follows:
[0031] (8) Install the drill bit, fix multiple drill bits on the multi-axis device according to the position of multiple insert holes in the workpiece window, and adjust the height difference of the drill bit according to the product size; and install the tapping drill correspondingly on the multi-axis device used for tapping ;
[0032] (9) Clamp the workpiece, fix the wheel product to be processed on the workpiece chuck, and adjust the coaxiality between the product and the fixture;
[0033] The present invention adopts a novel radial positioning structure, and three positioning structure components are radiall...
PUM
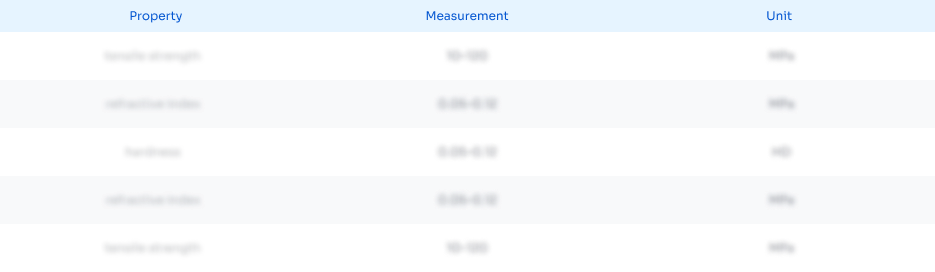
Abstract
Description
Claims
Application Information

- Generate Ideas
- Intellectual Property
- Life Sciences
- Materials
- Tech Scout
- Unparalleled Data Quality
- Higher Quality Content
- 60% Fewer Hallucinations
Browse by: Latest US Patents, China's latest patents, Technical Efficacy Thesaurus, Application Domain, Technology Topic, Popular Technical Reports.
© 2025 PatSnap. All rights reserved.Legal|Privacy policy|Modern Slavery Act Transparency Statement|Sitemap|About US| Contact US: help@patsnap.com