Mineral processing technology of refractory molybdenum ores with molybdenite and pyrite in close symbiotic relationship
A symbiotic relationship, pyrite technology, applied in the field of mineral processing, can solve the problems of poor flotation effect, long process flow, reduced recovery rate of filter press, etc., and achieve the effect of reducing the cost of mineral processing, improving technical indicators, and reducing the cost of mineral processing
- Summary
- Abstract
- Description
- Claims
- Application Information
AI Technical Summary
Problems solved by technology
Method used
Image
Examples
Embodiment Construction
[0039] The present invention will be described in further detail below in conjunction with the accompanying drawings and specific embodiments.
[0040] The flow chart of the beneficiation process of the refractory molybdenum ore closely related to molybdenite and pyrite symbiosis of the present invention is as figure 1 shown, including the following steps: For dosing point.
[0041] (1) The ore is crushed through the second stage and one closed-circuit crushing process to obtain crushed material, and the particle size of the grinding mill reaches -15mm;
[0042] (2) The crushed material adopts two stages and two closed-circuit processes to obtain ore pulp, and the grinding fineness is -200 mesh, accounting for 85%;
[0043] (3) The ore pulp is mixed and roughed and swept three times to obtain qualified tailings; the roughed concentrate is ground again, with a fineness of -325 mesh accounting for 85%, and then mixed three times to get the mixed concentrate; the pulp is mixed...
PUM
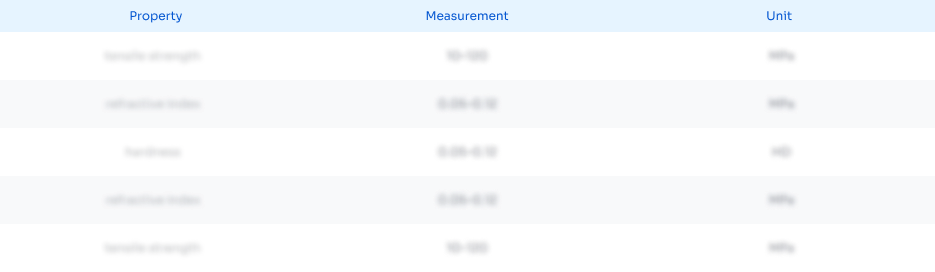
Abstract
Description
Claims
Application Information

- Generate Ideas
- Intellectual Property
- Life Sciences
- Materials
- Tech Scout
- Unparalleled Data Quality
- Higher Quality Content
- 60% Fewer Hallucinations
Browse by: Latest US Patents, China's latest patents, Technical Efficacy Thesaurus, Application Domain, Technology Topic, Popular Technical Reports.
© 2025 PatSnap. All rights reserved.Legal|Privacy policy|Modern Slavery Act Transparency Statement|Sitemap|About US| Contact US: help@patsnap.com