A kind of organic fluorine modified epoxy led packaging material and preparation method thereof
A technology of LED encapsulation and organic fluorine, which is applied in the direction of electrical components, circuits, semiconductor devices, etc., can solve the problems of poor compatibility, failure to take into account the light transmittance of materials, and large interfacial tension, and achieve excellent weather resistance and mechanical strength. Reduce the defect problem of phase separation between organic fluorine and epoxy resin, and effectively disperse the effect
- Summary
- Abstract
- Description
- Claims
- Application Information
AI Technical Summary
Problems solved by technology
Method used
Image
Examples
Embodiment 1
[0042] (1) Preparation of fluorine-containing and epoxy-based resins
[0043] (1-1) Add 15 g of dodecafluoroheptyl methacrylate (CH 2 =C(CH 3 ) COOCH 2 (CF 2 ) 5 CHF 2 ), 15g of 1,2-epoxy-5-hexene and 45ml of organic solvent butanone, stir evenly (stirring speed is 300rpm), pass into N 2 and heated to 70°C to obtain solution A;
[0044] (1-2) 0.90g of azobisisoheptanonitrile (ABVN) was dissolved in 18ml of butanone to obtain solution B;
[0045] (1-3) Divide solution B into three parts, add the first part of solution B (12mL) to solution A, and react at 70°C for 1h; then add the second portion of solution B (3mL), and continue to react at 70°C for 2h ; Finally, add the third solution B (3mL), continue to react at 70°C for 3h, cool down, use a rotary evaporator to remove the solvent and by-products at 80°C for 15min, then dissolve the rotary evaporated product in CH 2 Cl 2 , washed with water until neutral, dried over anhydrous magnesium sulfate, and continued rotary e...
Embodiment 2
[0051] (1) Preparation of fluorine-containing and epoxy-based resins
[0052] (1-1) Add 20g of hexafluorobutyl methacrylate (CH 2 =C(CH 3 ) COOCH 2 CF 2 CHFCF 3 ), 1.2g of glycidyl methacrylate and 30ml of organic solvent 1,4-dioxane, stir evenly (stirring speed is 400rpm), pass into N 2 and heated to 85°C to obtain solution A;
[0053] (1-2) Dissolve 0.848g of azobisisobutylcyanide (AIBN) in 12ml of organic solvent 1,4-dioxane, and mix well to obtain solution B;
[0054] (1-3) Divide solution B into three parts, add the first part of solution B (8mL) to solution A, and react at 85°C for 1h; then add the second portion of solution B (2mL), and continue to react at 85°C for 3h ; Finally, add the third solution B (2mL), continue to react at 85°C for 3h, cool to room temperature, use a rotary evaporator to remove the solvent and by-products at 80°C for 10min, then dissolve the rotary evaporated product in CH 2 Cl 2 , washed with water until neutral, dried over anhydrous m...
Embodiment 3
[0060] (1) Preparation of fluorine-containing and epoxy-based resins
[0061] (1-1) Add 8 g of trifluoroethyl methacrylate (CH 2 =C(CH 3 ) COOCH 2 CF 3 ), 15g of allyl glycidyl ether and 35ml organic solvent toluene, stir evenly (stirring speed is 400rpm), pass into N 2 and heated to 85°C to obtain solution A;
[0062] (1-2) Dissolve 0.52g of dibenzoyl peroxide (BPO) in 12ml of toluene, mix well to obtain solution B;
[0063] (1-3) Divide solution B into three parts, add the first part of solution B (8mL) to solution A, and react at 85°C for 1h; then add the second portion of solution B (2mL), and continue to react at 85°C for 2h ; Finally, add the third solution B (2mL), continue to react at 85°C for 3h, cool to room temperature, use a rotary evaporator to remove the solvent and by-products at 80°C for 15min, then dissolve the rotary evaporated product in CH 2 Cl 2 , washed with water until neutral, dried over anhydrous magnesium sulfate, and continued rotary evaporati...
PUM
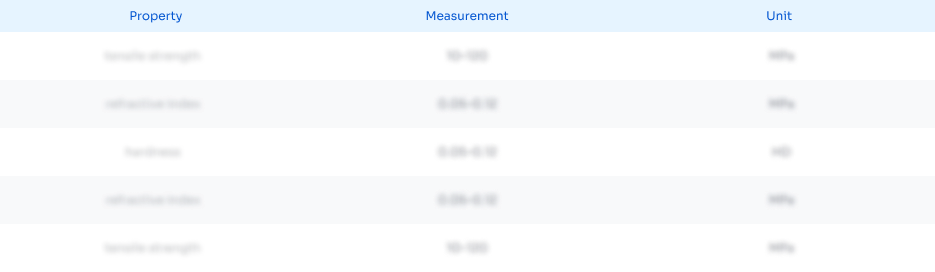
Abstract
Description
Claims
Application Information

- R&D
- Intellectual Property
- Life Sciences
- Materials
- Tech Scout
- Unparalleled Data Quality
- Higher Quality Content
- 60% Fewer Hallucinations
Browse by: Latest US Patents, China's latest patents, Technical Efficacy Thesaurus, Application Domain, Technology Topic, Popular Technical Reports.
© 2025 PatSnap. All rights reserved.Legal|Privacy policy|Modern Slavery Act Transparency Statement|Sitemap|About US| Contact US: help@patsnap.com