Five-axis hub transfer robot and clamping manipulator
A technology for handling robots and manipulators. It is applied in the direction of conveyor objects, transportation and packaging. It can solve the problems of expensive equipment, easy to damage the surface of the wheel hub, and high labor intensity. It achieves stable and reliable picking and clamping, and reduces the waiting time for material preparation. , The effect of speeding up the production tempo
- Summary
- Abstract
- Description
- Claims
- Application Information
AI Technical Summary
Problems solved by technology
Method used
Image
Examples
Embodiment Construction
[0024] The specific implementation manner of the present invention will be described below in conjunction with the accompanying drawings.
[0025] like figure 1 As shown, the wheel hub five-axis handling robot of the present invention includes a truss 1, an X-axis drive system 2, a Y-axis drive system 3, a Z-axis drive system 4, a C-axis drive system 5, an A-axis drive system 6 and a clamping manipulator 7. The X-axis driving system 2 is installed on the truss 1, and the Y-axis driving system 3 is installed across the X-axis driving system 2 through the XY-axis connecting plate 12. The Z-axis driving system 4 is vertically installed on the Y-axis through the YZ-axis connecting plate 16. Drive system 3, X-axis drive system 2, Y-axis drive system 3, and Z-axis drive system 4 are orthogonal to each other, forming an XYZ Cartesian coordinate robot to realize the transportation of wheels between different production lines, as well as between the handling robot and wheel hub proces...
PUM
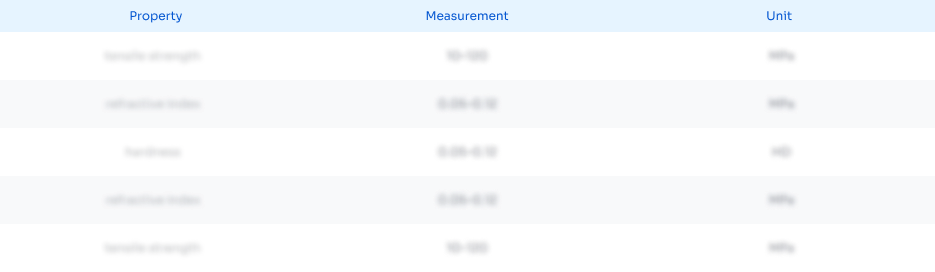
Abstract
Description
Claims
Application Information

- Generate Ideas
- Intellectual Property
- Life Sciences
- Materials
- Tech Scout
- Unparalleled Data Quality
- Higher Quality Content
- 60% Fewer Hallucinations
Browse by: Latest US Patents, China's latest patents, Technical Efficacy Thesaurus, Application Domain, Technology Topic, Popular Technical Reports.
© 2025 PatSnap. All rights reserved.Legal|Privacy policy|Modern Slavery Act Transparency Statement|Sitemap|About US| Contact US: help@patsnap.com