A non-contact energy transfer device for rotary ultrasonic machining
A rotary ultrasonic and energy transmission technology, applied in positioning devices, metal processing equipment, fluids using vibration, etc., can solve the problems of reducing the automation level of processing efficiency, large transformation costs and capital investment, and adverse processing safety. Preparation time, increased automation level, improved machining efficiency and effect of automation level
- Summary
- Abstract
- Description
- Claims
- Application Information
AI Technical Summary
Problems solved by technology
Method used
Image
Examples
Embodiment 1
[0041] Such as figure 1 , 2 , 3, and 4 are schematic diagrams of Embodiment 1 of the axially open non-contact energy transmission device of the present invention. Among them, in addition to the adjustment mechanism and the rotating ultrasonic handle, the openness of the core non-contact energy transmission device is mainly reflected in the magnetic core structure and winding method: in this embodiment, an axially open non-contact energy transmission device is used . In terms of magnetic core structure, the fixed-end magnetic core 2 and the rotating-end magnetic core 5 adopt partial and complete pot-shaped magnetic cores respectively. The two are coaxial and arranged with a small gap between the axes. The effective area A passing through the lines of magnetic field e In the same way, an open magnetic field circuit is formed; in the winding method, the fixed-end coil 3 is wound on the outer wall of the fixed-end magnetic core 3, and the rotating-end coil 4 is wound in the gr...
Embodiment 2
[0043] Such as Figure 5 , 6 , 7, and 8 are schematic diagrams of Embodiment 2 of the radially open non-contact energy transmission device of the present invention, which are the same as figure 1 , 2 , 3, and 4 show the similarities between the adjustment mechanism and the rotating ultrasonic knife handle in Embodiment 1, so the description will not be repeated, and only the differences will be described.
[0044] In the second embodiment, a radially open non-contact energy transmission device is used. Its openness is reflected in: in the magnetic core structure, the fixed-end magnetic core 2 and the rotating-end magnetic core 5 adopt part and the whole slotted annular magnetic core respectively, and the two are coaxial and arranged with small radial gaps. It is the same as the effective area Ae of the rotating end magnetic core 5 through the magnetic induction line, forming an open magnetic field circuit; in the winding mode, the fixed end coil 3 is wound on the outer wal...
PUM
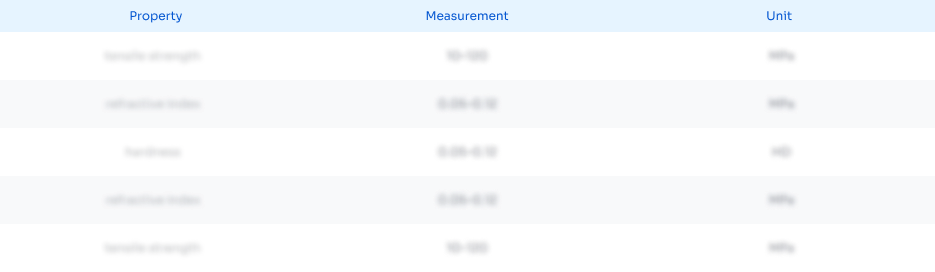
Abstract
Description
Claims
Application Information

- Generate Ideas
- Intellectual Property
- Life Sciences
- Materials
- Tech Scout
- Unparalleled Data Quality
- Higher Quality Content
- 60% Fewer Hallucinations
Browse by: Latest US Patents, China's latest patents, Technical Efficacy Thesaurus, Application Domain, Technology Topic, Popular Technical Reports.
© 2025 PatSnap. All rights reserved.Legal|Privacy policy|Modern Slavery Act Transparency Statement|Sitemap|About US| Contact US: help@patsnap.com