Processing device and processing method of high-iron silicon carbide micropowder
A silicon carbide micropowder and processing method technology, which is applied in the field of high-iron silicon carbide micropowder processing devices, can solve the problems of pollution, long time required, and difficulty in processing high-iron materials, so as to avoid environmental pollution, fully react, and shorten the production cycle Effect
- Summary
- Abstract
- Description
- Claims
- Application Information
AI Technical Summary
Problems solved by technology
Method used
Image
Examples
Embodiment 1
[0027] Embodiment 1: a kind of high-iron silicon carbide micropowder processing device, such as figure 1 , figure 2 As shown, it includes a reaction barrel 1 and an ultrasonic device, the upper part of the reaction barrel 1 is provided with a feed port 2, and the lower part is provided with a discharge port 3, and the ultrasonic device includes at least one ultrasonic oscillator 4 arranged on the outer wall of the reaction barrel 1, And at least one ultrasonic generator 5 arranged outside the reaction barrel 1 , each ultrasonic generator 5 is connected with two ultrasonic oscillators; a stirrer 6 is also arranged in the reaction barrel 1 . Wherein, the ultrasonic generator and the ultrasonic oscillator are connected through a high-frequency line with a socket; the reaction barrel 1 is made of stainless steel.
Embodiment 2
[0028] Embodiment 2: A kind of high-iron silicon carbide micropowder processing device, the difference with embodiment 1 is that a temperature sensor is also arranged in the reaction barrel 1, and a heater is also arranged on the inner wall of the reaction barrel 1 (not shown in the accompanying drawings). draw).
Embodiment 3
[0029] Embodiment 3: a kind of processing method of high-iron silicon carbide micropowder comprises the following steps:
[0030] (1) Mixing: Introduce the high-iron silicon carbide micropowder produced by the magnetic separator into the reaction tank of the high-iron silicon carbide micropowder processing device in Example 2, add hot water at 90°C, stir evenly, and obtain a mass percent concentration of 20 % of slurry;
[0031] (2) Ultrasonic oscillation: Turn on the ultrasonic equipment, and under the condition of ultrasonic frequency of 40KHz, perform ultrasonic oscillation treatment on the slurry in the reaction tank for 30 minutes, and turn on the agitator while performing ultrasonic oscillation treatment, and the material in the reaction tank slurry for stirring;
[0032] (3) Acid leaching: To the slurry obtained in step (2), add an acid accounting for 30% of the slurry volume fraction, and carry out an acid leaching reaction for 5 hours at a reaction temperature of 80°...
PUM
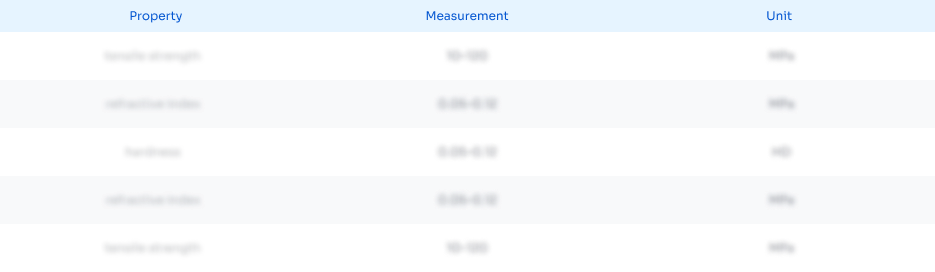
Abstract
Description
Claims
Application Information

- R&D
- Intellectual Property
- Life Sciences
- Materials
- Tech Scout
- Unparalleled Data Quality
- Higher Quality Content
- 60% Fewer Hallucinations
Browse by: Latest US Patents, China's latest patents, Technical Efficacy Thesaurus, Application Domain, Technology Topic, Popular Technical Reports.
© 2025 PatSnap. All rights reserved.Legal|Privacy policy|Modern Slavery Act Transparency Statement|Sitemap|About US| Contact US: help@patsnap.com