CCD-based method for automatic identification and trajectory planning of pipe space welds
An automatic identification and trajectory planning technology, applied in welding equipment, auxiliary welding equipment, welding/cutting auxiliary equipment, etc., can solve the problems of inability to weld, unsuitable space welds, rare research and application, etc., to reduce labor force , Avoid limitations, reduce manufacturing cost and time cost effect
- Summary
- Abstract
- Description
- Claims
- Application Information
AI Technical Summary
Problems solved by technology
Method used
Image
Examples
Embodiment Construction
[0032] In order to make the purpose, technical solutions and beneficial effects of the present invention clearer, the present invention will be further described in detail below in conjunction with specific embodiments and with reference to the accompanying drawings, but the implementation of the present invention is not limited thereto.
[0033] The CCD-based automatic identification and trajectory planning method of pipeline space welds in the present invention comprises the following steps:
[0034] (1) Select the welding module: select pipe-pipe butt joint or pipe-pipe intersecting welding on the main control computer;
[0035] (2) Collect pictures of workpieces to be welded: adopt the method of "one eye and two positions" to collect pictures of workpieces to be welded, the main control computer sends signals to the welding robot, and the welding robot moves to 6 different shooting positions successively. The specific shooting positions are as follows: figure 1 As shown, t...
PUM
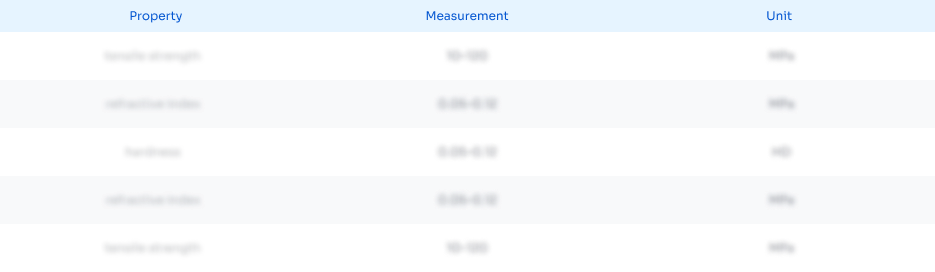
Abstract
Description
Claims
Application Information

- R&D Engineer
- R&D Manager
- IP Professional
- Industry Leading Data Capabilities
- Powerful AI technology
- Patent DNA Extraction
Browse by: Latest US Patents, China's latest patents, Technical Efficacy Thesaurus, Application Domain, Technology Topic, Popular Technical Reports.
© 2024 PatSnap. All rights reserved.Legal|Privacy policy|Modern Slavery Act Transparency Statement|Sitemap|About US| Contact US: help@patsnap.com