Electric furnace production process of high-purity non-quenched and tempered steel for crankshaft
A production process, non-quenching and tempering technology, applied in the field of metallurgy, can solve the problems of low material utilization rate, cumbersome processing process, low success rate, etc., and achieve the effect of good cutting performance, high purity, uniform composition and low-magnification structure
- Summary
- Abstract
- Description
- Claims
- Application Information
AI Technical Summary
Problems solved by technology
Method used
Examples
Embodiment 1
[0018] This example is an electric furnace production process of high-purity non-quenched and tempered crankshaft steel. The mass percentage composition of high-purity non-quenched and tempered crankshaft steel is: C: 0.45%, Mn: 1.02%, P: 0.025%, S: 0.020%, Si: 0.20%, Cr: 0.05%, Alt: 0.015%, V: 0.07%, Ti: 0.025%, Ni: 0.20%, Cu: 0.04%, Mo: 0.01%, N: 0.0080%, O: 0.0020%, Ceq: 0.88%, the balance is Fe;
[0019] The technological process of the electric furnace production process of high-purity non-quenched and tempered crankshaft steel is: scrap steel + hot charging molten iron → EBT electric arc furnace smelting → LF refining → VD vacuum degassing treatment → continuous casting and pouring into billets;
[0020] During the smelting and tapping process of EBT electric arc furnace, manganese nitride alloy is used to control the N content in molten steel within the range of 200ppm, and other elements except S and Alt are adjusted to 85% of the lower limit of the judgment range by u...
Embodiment 2
[0025] This example is an electric furnace production process of high-purity non-quenched and tempered crankshaft steel. The mass percentage composition of high-purity non-quenched and tempered crankshaft steel is: C: 0.46%, Mn: 1.08%, P: 0.02%, S: 0.025%, Si: 0.25%, Cr: 0.1%, Alt: 0.025%, V: 0.09%, Ti: 0.02%, Ni: 0.1%, Cu: 0.1%, Mo: 0.03%, N: 0.01%, O: 0.001%, Ceq: 0.92%, the balance is Fe;
[0026] The technological process of the electric furnace production process of high-purity non-quenched and tempered crankshaft steel is: scrap steel + hot charging molten iron → EBT electric arc furnace smelting → LF refining → VD vacuum degassing treatment → continuous casting and pouring into billets;
[0027] During the smelting and tapping process of EBT electric arc furnace, manganese nitride alloy is used to control the N content in molten steel within the range of 250ppm, and other elements except S and Alt are adjusted to 85% of the lower limit of the judgment range by using corre...
Embodiment 3
[0032] This example is an electric furnace production process of high-purity non-quenched and tempered crankshaft steel. The mass percentage composition of high-purity non-quenched and tempered crankshaft steel is: C: 0.48%, Mn: 1.12%, P: 0.01%, S: 0.030%, Si: 0.30%, Cr: 0.25%, Alt: 0.035%, V: 0.12%, Ti: 0.01%, Ni: 0.09%, Cu: 0.15%, Mo: 0.05%, N: 0.0140%, O: 0.001%, Ceq: 0.96%, the balance is Fe;
[0033] The technological process of the electric furnace production process of high-purity non-quenched and tempered crankshaft steel is: scrap steel + hot charging molten iron → EBT electric arc furnace smelting → LF refining → VD vacuum degassing treatment → continuous casting and pouring into billets;
[0034] During the smelting and tapping process of EBT electric arc furnace, manganese nitride alloy is used to control the N content in molten steel within the range of 280ppm, and other elements except S and Alt are adjusted to 85% of the lower limit of the judgment range by usin...
PUM
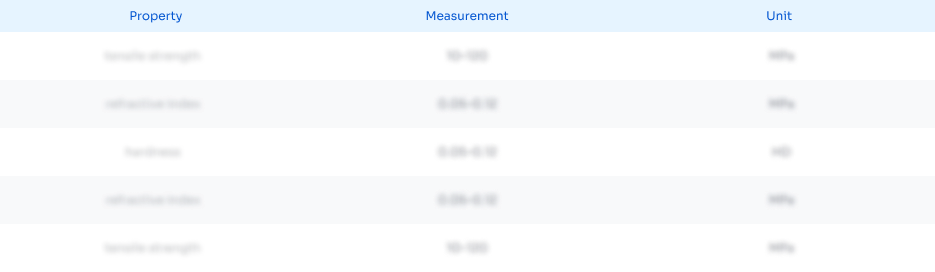
Abstract
Description
Claims
Application Information

- Generate Ideas
- Intellectual Property
- Life Sciences
- Materials
- Tech Scout
- Unparalleled Data Quality
- Higher Quality Content
- 60% Fewer Hallucinations
Browse by: Latest US Patents, China's latest patents, Technical Efficacy Thesaurus, Application Domain, Technology Topic, Popular Technical Reports.
© 2025 PatSnap. All rights reserved.Legal|Privacy policy|Modern Slavery Act Transparency Statement|Sitemap|About US| Contact US: help@patsnap.com