Cellulose acetate butyrate mixed ester with high butyryl content, and preparation method thereof
A technology of cellulose mixed ester and acetic acid butyric acid is applied in the preparation of cellulose acetate butyrate mixed ester and the field of cellulose acetate butyrate mixed ester, which can solve the problem of low cellulose efficiency, low butyryl content, long reaction time, etc. problem, to achieve the effect of less dosage, good effect and short preparation period
- Summary
- Abstract
- Description
- Claims
- Application Information
AI Technical Summary
Problems solved by technology
Method used
Examples
Embodiment 1
[0028] A cellulose acetate butyrate mixed ester with high butyryl content comprises the following components: 600 kg of wood pulp, 980 kg of butyric acid, 2745 kg of butyric anhydride, 24 kg of acetic anhydride, and 30 kg of concentrated sulfuric acid catalyst.
[0029] The above method for preparing cellulose acetate butyrate mixed ester with high butyryl content is innovative in that it specifically comprises the following steps:
[0030] (1) The proportioned wood pulp is first sprayed with 370kg of butyric acid, and then activated at 25°C for 12 hours to become solid;
[0031] (2) Mix the remaining amount of butyric acid with the matching amount of butyric anhydride, acetic anhydride, and concentrated sulfuric acid catalyst, and cool the mixture to 3°C for use;
[0032] (3) Put the activated solid in step (1) into the cooling liquid of step (2) within 5 minutes, stir fully, adjust the cooling amount of the cooling liquid to control the reaction heating rate, so that the tem...
Embodiment 2
[0038] On the basis of embodiment 1, change the content of the concentrated sulfuric acid catalyst in the composition, specifically as follows: wood pulp 600kg, butyric acid 980kg, butyric anhydride 2745kg, acetic anhydride 24kg, 60kg concentrated sulfuric acid catalyst. Adopt the preparation method of embodiment 1 to prepare, obtain product.
[0039] In this example, cellulose acetate butyrate with a butyryl content of 52% and an acetyl content of 2.5% was obtained, and the product performance was stable.
Embodiment 3
[0041] On the basis of Example 1 or 2, using the ratio of raw materials in Example 1 or 2, the wood pulp in the raw material is pulverized to ensure that the length of the short fluff after pulverization is ≤ 1mm, and the hydrolysis reaction process is controlled before the start of the process. , Control the initial water content of the reaction system at 5% to 10%. Adopt the preparation method of embodiment 1 to prepare, obtain product.
[0042] In this example, cellulose acetate butyrate with a butyryl content of 52% and an acetyl content of 3% was obtained, and the product performance was stable.
PUM
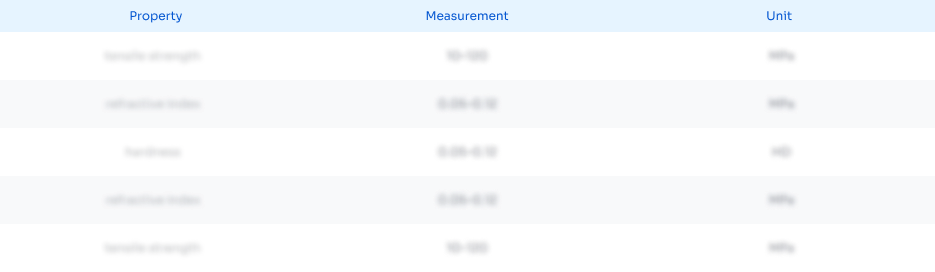
Abstract
Description
Claims
Application Information

- R&D
- Intellectual Property
- Life Sciences
- Materials
- Tech Scout
- Unparalleled Data Quality
- Higher Quality Content
- 60% Fewer Hallucinations
Browse by: Latest US Patents, China's latest patents, Technical Efficacy Thesaurus, Application Domain, Technology Topic, Popular Technical Reports.
© 2025 PatSnap. All rights reserved.Legal|Privacy policy|Modern Slavery Act Transparency Statement|Sitemap|About US| Contact US: help@patsnap.com