Method for improving inapplicable upper tobacco leaf raw material quality
A technology of tobacco leaves and raw materials, which is applied in the field of improving the quality of unsuitable upper tobacco leaf raw materials, can solve the problems of poor quality of upper tobacco leaf raw materials, negative impact on sensory quality, low utilization rate, etc., and achieve fine smoke, improvement of internal sensory quality indicators, The effect of alleviating inventory pressure
- Summary
- Abstract
- Description
- Claims
- Application Information
AI Technical Summary
Problems solved by technology
Method used
Image
Examples
Embodiment 1
[0031] 1. Processing method
[0032] Weigh 2kg of shredded tobacco B3K (upper variegated color grade 3) produced in Zhangjiajie, Hunan Province in 2012 after storage and alcoholization, put it into a 25-liter airtight glass container, add 10kg of ethanol solution with a volume concentration of 70%, and let it stand at a temperature of 50°C After processing for 30 minutes, under the vacuum condition of -0.050~-0.055Mpa (at this time, there are bubbles coming out of the processing solvent), the solid-liquid separation is carried out after 15 minutes of reduced pressure treatment, and the shredded tobacco is taken out and dried at 50°C until the water content is 12.5 wt%. Sampling for detection analysis and sensory evaluation.
[0033] 2. Test results:
[0034] (1), main chemical components of shredded tobacco
[0035] Table 1 below shows the results of detecting the main chemical components in shredded tobacco before and after treatment by using a fluid analyzer according to ...
Embodiment 2
[0043] 1. Processing method
[0044] Weigh 2.2kg of B2K (upper variegated second-grade grade 2) cigarette produced in Hunan Xiangxi Autonomous Prefecture in 2012 after storage and alcoholization, put it into a 25-liter airtight glass container, add 11kg of ethanol solution with a volume concentration of 35%, and store it at a temperature of 65°C. After standing still for 30 minutes, under the vacuum condition of -0.035~-0.045Mpa (at this time, there are bubbles in the processing solvent), the solid-liquid separation is carried out after 10 minutes of decompression treatment, and the solid-liquid separation is carried out. Preliminary drying under conditions to a water content of 22wt% was taken out and cut into shreds, and then dried to a water content of 12wt% before sampling for detection, analysis and sensory evaluation.
[0045] 2. Test results:
[0046] (1), the main chemical components of tobacco leaves
[0047] Table 3 below shows the results of the main chemical comp...
Embodiment 3
[0055] 1. Processing method
[0056] Weigh 40g cut tobacco produced in Yongshun, Xiangxi, Hunan in 2011, after storage and alcoholization, put it into a 1-liter airtight glass container, and process it one by one according to the conditions described in Table 5; then separate solid-liquid, cut tobacco After taking it out, dry it at 50°C until the water content is 12.5wt%, take it out, and take a sample for sensory evaluation.
[0057] Table 5 Orthogonal design table of experimental treatments for improving the quality of upper unsuitable tobacco leaves
[0058]
[0059] 2. Intrinsic sensory quality of each processed cut tobacco sample
[0060] Compared with the unsuitable upper tobacco leaf material (control sample) without any treatment, 1-9 in Table 5 treated the unsuitable upper tobacco leaf raw material, the aroma of the treated sample was brighter, and the degree of dry coke gas and nitrogen-containing impurities was obvious Reduced, vigor was significantly reduced, ...
PUM
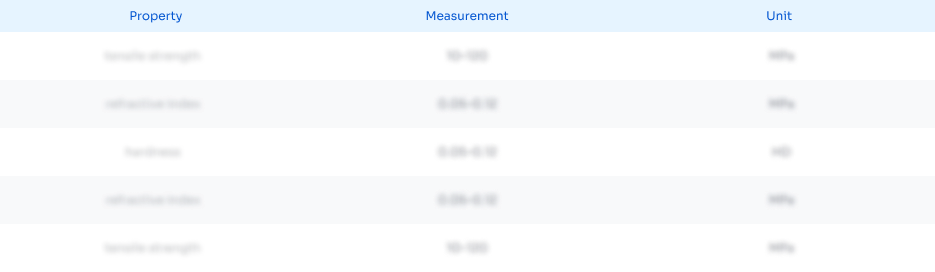
Abstract
Description
Claims
Application Information

- R&D
- Intellectual Property
- Life Sciences
- Materials
- Tech Scout
- Unparalleled Data Quality
- Higher Quality Content
- 60% Fewer Hallucinations
Browse by: Latest US Patents, China's latest patents, Technical Efficacy Thesaurus, Application Domain, Technology Topic, Popular Technical Reports.
© 2025 PatSnap. All rights reserved.Legal|Privacy policy|Modern Slavery Act Transparency Statement|Sitemap|About US| Contact US: help@patsnap.com