Preparation method of porous tin-carbon composite negative material
A composite material, tin-carbon technology, applied in the direction of non-aqueous electrolyte battery electrodes, electrical components, electrochemical generators, etc., can solve the problems of large volume change, structural collapse, loss of electrochemical activity, etc., to achieve wide distribution and low price Effect
- Summary
- Abstract
- Description
- Claims
- Application Information
AI Technical Summary
Problems solved by technology
Method used
Image
Examples
Embodiment 1
[0025] A method for preparing a porous tin-carbon composite material, comprising the following preparation steps:
[0026] A. Put tin oxide, sucrose and sodium carbonate into a ball mill tank according to the amount of substances = 1:1:1, and ball mill at 300 rpm for 4 hours to obtain a mixed precursor;
[0027] B. Place the precursor in a flowing nitrogen atmosphere in a tube furnace and other devices, raise the temperature to 600°C at a heating rate of 3°C / min, keep it warm for 6 hours, and cool to room temperature with the furnace;
[0028] C. The obtained calcined product was washed with deionized water, then centrifuged, washed several times, and dried at 80°C to obtain a porous tin-carbon composite material.
Embodiment 2
[0030] A method for preparing a porous tin-carbon composite material, comprising the following preparation steps:
[0031] A. Put tin oxide, glucose and lithium carbonate into a ball mill tank according to the amount of substances = 0.6:1.2:1.2, and ball mill for 1 hour at 400 rpm to obtain a mixed precursor;
[0032] B. Place the precursor in a flowing nitrogen atmosphere in a tube furnace and other devices, raise the temperature to 500°C at a heating rate of 5°C / min, keep it warm for 1 hour, and cool to room temperature with the furnace;
[0033] C. The obtained calcined product was washed with deionized water, then centrifuged, washed several times, and dried at 50°C to obtain a porous tin-carbon composite material.
Embodiment 3
[0035] A method for preparing a porous tin-carbon composite material, comprising the following preparation steps:
[0036] A. Put tin oxide, graphite and sodium carbonate into a ball mill jar according to the amount of substances = 2.8:0.1:0.1, and ball mill at 200 rpm for 12 hours to obtain a mixed precursor;
[0037] B. Place the precursor in a flowing nitrogen atmosphere in a tube furnace and other devices, raise the temperature to 1000°C at a heating rate of 2°C / min, keep it warm for 3 hours, and cool to room temperature with the furnace;
[0038] C. The obtained calcined product was washed with deionized water, then centrifuged, washed several times, and dried at 100°C to obtain a porous tin-carbon composite material.
PUM
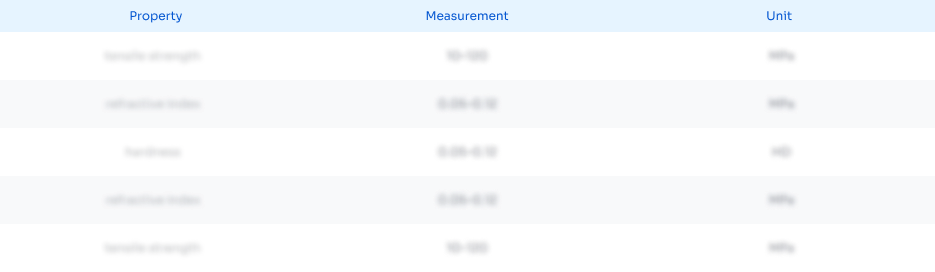
Abstract
Description
Claims
Application Information

- R&D
- Intellectual Property
- Life Sciences
- Materials
- Tech Scout
- Unparalleled Data Quality
- Higher Quality Content
- 60% Fewer Hallucinations
Browse by: Latest US Patents, China's latest patents, Technical Efficacy Thesaurus, Application Domain, Technology Topic, Popular Technical Reports.
© 2025 PatSnap. All rights reserved.Legal|Privacy policy|Modern Slavery Act Transparency Statement|Sitemap|About US| Contact US: help@patsnap.com