A kind of preparation method of porous carbon nanofiber felt and porous carbon nanofiber electrode
A nanofiber and porous carbon technology is applied in the field of preparation of porous carbon nanofiber felt and porous carbon nanofiber electrode, which can solve the problems of pollution, increase in production cost, consumption of energy and reagent raw materials, etc., so as to reduce costs and simplify the operation process. , good electrochemical performance and desalination effect
- Summary
- Abstract
- Description
- Claims
- Application Information
AI Technical Summary
Problems solved by technology
Method used
Image
Examples
Embodiment 1
[0034] Weigh 0.9371g polyacrylonitrile (PAN; M w =150000), add in 10mL dimethylformamide (DMF); add 1.4056g dimethyl sulfone (DMSO2), 60 ℃ of constant temperature water baths are heated until completely dissolving, be mixed with PAN concentration and be 9%, PAN and DMSO Mass ratio is 2:3 spinning precursor solution. The precursor solution placed in a 10mL needle tube was pushed into a 12kV electrostatic field through a needle with a diameter of 0.5mm at a constant rate of 1mL / min by a quantitative pump for electrospinning. The distance between the receiving plate and the needle was 15cm, and the ambient temperature was 20.5°C. The relative humidity is 35%. The nanofiber mat obtained by electrospinning was placed in a muffle furnace, and the temperature was raised from room temperature to 80 °C at a rate of 1 °C / min in an air atmosphere, stayed for 1 h, and then raised to 260 °C at a rate of 1 °C / min. ℃ and stay for 1h to complete the pre-oxidation pore-forming process, figu...
Embodiment 2
[0035] Embodiment two (control test)
[0036] Weigh 0.9371g polyacrylonitrile (PAN; M w =150000), add 10mL of dimethylformamide (DMF) in a 60°C constant temperature water bath and heat until completely dissolved to prepare a spinning precursor solution with a PAN concentration of 9%. Use a quantitative pump to push the precursor solution in a 10mL needle tube into a 12kV electrostatic field through a needle with a diameter of 0.5mm at a constant rate of 1mL / min. The distance between the receiving plate and the needle is 15cm, the ambient temperature is 28°C, and the relative humidity is 35 %. The nanofiber mat obtained by electrospinning was placed in a muffle furnace, and the temperature was raised from room temperature to 80 °C at a rate of 1 °C / min in an air atmosphere, stayed for 1 h, and then raised to 260 °C at a rate of 1 °C / min. ℃ and stay for 1h to complete the pre-oxidation process. Under a nitrogen atmosphere, place the pre-oxidized nanofiber mat in a tube furnac...
Embodiment 3
[0038] Weigh 0.9371g polyacrylonitrile (PAN; M w =150000), add in 10mL dimethylformamide (DMF); add 0.6264g dimethyl sulfone, heat in a constant temperature water bath at 60°C until completely dissolved, and prepare the PAN concentration as 9%, and the mass ratio of PAN to DMSO2 is 3:2 spinning precursors. The precursor solution placed in a 10mL needle tube was pushed into a 12kV electrostatic field through a needle with a diameter of 0.5mm at a constant rate of 1mL / min by a quantitative pump for electrospinning. The distance between the receiving plate and the needle was 15cm, and the ambient temperature was 29°C. The relative humidity is 32%. The nanofiber mat obtained by electrospinning was placed in a muffle furnace, and the temperature was raised from room temperature to 80 °C at a rate of 1 °C / min in an air atmosphere, stayed for 1 h, and then raised to 260 °C at a rate of 1 °C / min. °C and stay for 1h to complete the pre-oxidation pore-forming process. Under a nitroge...
PUM
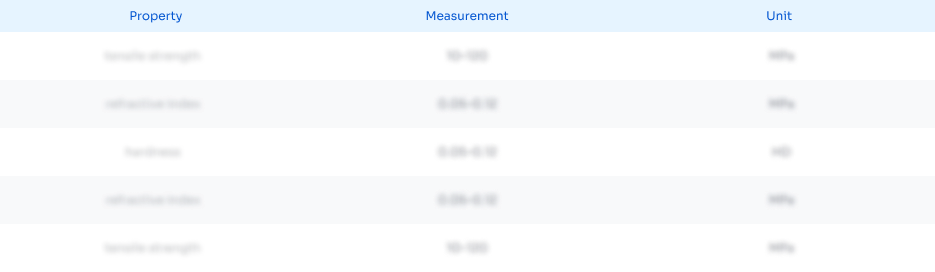
Abstract
Description
Claims
Application Information

- R&D
- Intellectual Property
- Life Sciences
- Materials
- Tech Scout
- Unparalleled Data Quality
- Higher Quality Content
- 60% Fewer Hallucinations
Browse by: Latest US Patents, China's latest patents, Technical Efficacy Thesaurus, Application Domain, Technology Topic, Popular Technical Reports.
© 2025 PatSnap. All rights reserved.Legal|Privacy policy|Modern Slavery Act Transparency Statement|Sitemap|About US| Contact US: help@patsnap.com