Technique for firing spinel-type black ceramic material with tunnel kiln
A black ceramic pigment and spinel-type technology, which is applied to the process field of firing spinel-type black ceramic materials in a tunnel kiln, can solve the problems of high energy consumption and low production capacity, and achieves strong color development ability and low cost. Low, high productivity
- Summary
- Abstract
- Description
- Claims
- Application Information
AI Technical Summary
Problems solved by technology
Method used
Examples
Embodiment 1
[0038] The technique of firing the spinel type black ceramic pigment with the tunnel kiln of the present embodiment comprises the steps:
[0039] 1) Mix the matrix raw materials chromium oxide green, iron oxide red, cobalt oxide, and nickel oxide in a mass ratio of 30:38:18:14 evenly;
[0040] 2) Put the above mixture into a sagger, load 8 minutes full, stack the saggers crosswise, place them in the traditional gas shuttle kiln and tunnel kiln for calcination respectively;
[0041] Calcination process of gas shuttle kiln: 25℃-500℃, heating up 2H, 500℃-1000℃, heating up 3H, 1000℃-1250℃, heating up 3H; The particle size D90 is 13-18μm. denoted as C;
[0042] Tunnel kiln calcination process: preheating zone 1200°C, high temperature zone 1250°C; transmission speed: about 17H from feeding to discharging; ventilation creates negative pressure in the kiln, and finally cools naturally; denoted as D;
[0043] 3) Grinding the cooled calcined product, adding concentrated hydrochloric ...
Embodiment 2
[0058] The technique of firing the spinel type black ceramic pigment with the tunnel kiln of the present embodiment comprises the steps:
[0059] 1) Mix the matrix raw materials chromium oxide green, iron oxide red, cobalt oxide, and nickel oxide in a mass ratio of 30:38:18:14 evenly;
[0060] 2) Put the above mixture into a sagger, load 8 minutes full, stack the saggers crosswise, place them in a tunnel kiln for calcination, but adjust the atmosphere in the kiln separately, the experiment is as follows:
[0061] Tunnel kiln calcination, preheating zone 1200°C, high temperature zone 1250°C; transmission speed: about 17H from feeding to discharging; ventilation creates negative pressure in the kiln, and finally cools naturally; denoted as D;
[0062] Tunnel kiln calcination, preheating zone 1200°C, high temperature zone 1250°C; transmission speed: about 17H from feeding to discharging; there is no draft in the kiln, natural smoke exhaust, and finally natural cooling; denoted as...
Embodiment 3
[0074] The technique of firing the spinel type black ceramic pigment with the tunnel kiln of the present embodiment comprises the steps:
[0075] 1) Mix the matrix raw materials chromium oxide green, iron oxide red, cobalt oxide, and nickel oxide in a mass ratio of 25:30:25:20;
[0076] 2) Put the above mixture into a sagger, load 8 minutes full, stack the saggers crosswise, place them in a tunnel kiln for calcination, and the calcination process conditions are as follows:
[0077] The preheating zone is 1170°C, the high temperature zone is 1200°C; transmission speed: about 15H from feeding to discharging; the draft creates negative pressure in the kiln, and finally cools naturally;
[0078] 3) Grinding the cooled calcined product, adding concentrated hydrochloric acid to pickle the powder, the mass ratio of concentrated hydrochloric acid: powder: water is 2.5:100:50, stir after adding to make the reaction fully, then stir and wash with water until the pH is 7;
[0079] 4) St...
PUM
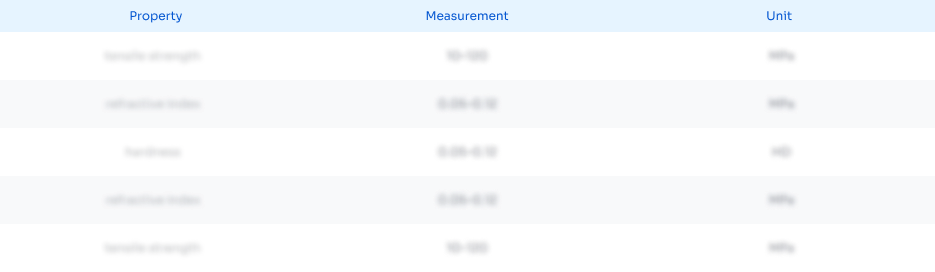
Abstract
Description
Claims
Application Information

- R&D Engineer
- R&D Manager
- IP Professional
- Industry Leading Data Capabilities
- Powerful AI technology
- Patent DNA Extraction
Browse by: Latest US Patents, China's latest patents, Technical Efficacy Thesaurus, Application Domain, Technology Topic, Popular Technical Reports.
© 2024 PatSnap. All rights reserved.Legal|Privacy policy|Modern Slavery Act Transparency Statement|Sitemap|About US| Contact US: help@patsnap.com