Air-drying protective paint for plastics and preparation method thereof
A self-drying, plastic technology, used in anti-corrosion coatings, coatings, etc., can solve the problems of long self-drying time, anti-corrosion, wear-resistant can not meet the requirements, can not apply plastic coating, etc., to achieve the effect of excellent performance
- Summary
- Abstract
- Description
- Claims
- Application Information
AI Technical Summary
Problems solved by technology
Method used
Image
Examples
Embodiment 1
[0020] A self-drying plastic protective coating, comprising in terms of weight components: 10 parts of butyl acrylate, 5 parts of light calcium carbonate, 1 part of talc, 2 parts of bentonite, 0.2 parts of silicone defoamer, ethylene carbonate 2 parts, 5 parts of ethyl 2-cyanoacrylate, 0.2 part of ethylene glycol monoethyl ether, 1 part of disodium succinate, 0.6 part of N-oleoyl sarcosine octadecylamine, and 20 parts of ethyl acetate.
[0021] The preparation method of the above-mentioned self-drying plastic protective coating is characterized in that the steps are as follows:
[0022] Step 1, add butyl acrylate, light calcium carbonate, bentonite, ethylene carbonate and ethyl acetate in the reactor with condenser, stirrer and thermostat, stir and heat to reflux, continue stirring for 60 minutes, above The stirring speed is 120 rev / min to obtain mixture 1;
[0023] Step 2, add ethyl 2-cyanoacrylate, ethylene glycol monoethyl ether and N-oleoyl sarcosine octadecylamine to mix...
Embodiment 2
[0026] A self-drying plastic protective coating, comprising in terms of weight components: 14 parts of butyl acrylate, 6 parts of light calcium carbonate, 3 parts of talcum powder, 3 parts of bentonite, 0.3 parts of silicone defoamer, ethylene carbonate 3 parts, 6 parts of ethyl 2-cyanoacrylate, 0.4 parts of ethylene glycol monoethyl ether, 2 parts of disodium succinate, 0.8 parts of N-oleoyl sarcosine octadecylamine, and 25 parts of ethyl acetate.
[0027] The preparation method of the above-mentioned self-drying plastic protective coating is characterized in that the steps are as follows:
[0028] Step 1, add butyl acrylate, light calcium carbonate, bentonite, ethylene carbonate and ethyl acetate in the reactor with condenser, stirrer and thermostat, stir and heat to reflux, continue stirring for 70 minutes, above The stirring speed is 130 rev / min to obtain mixture 1;
[0029] Step 2, add ethyl 2-cyanoacrylate, ethylene glycol monoethyl ether and N-oleoyl sarcosine octadecy...
Embodiment 3
[0032] A self-drying plastic protective coating, comprising in terms of weight components: 15 parts of butyl acrylate, 7 parts of light calcium carbonate, 4 parts of talcum powder, 4 parts of bentonite, 0.4 parts of silicone defoamer, ethylene carbonate 4 parts, 7 parts of ethyl 2-cyanoacrylate, 0.5 parts of ethylene glycol monoethyl ether, 3 parts of disodium succinate, 1.5 parts of N-oleoyl sarcosine octadecylamine, and 27 parts of ethyl acetate.
[0033] The preparation method of the above-mentioned self-drying plastic protective coating is characterized in that the steps are as follows:
[0034] Step 1, add butyl acrylate, light calcium carbonate, bentonite, ethylene carbonate and ethyl acetate in the reactor with condenser, stirrer and thermostat, stir and heat to reflux, continue stirring for 80 minutes, above The stirring speed is 130 rev / min to obtain mixture 1;
[0035] Step 2, add ethyl 2-cyanoacrylate, ethylene glycol monoethyl ether and N-oleoyl sarcosine octadecy...
PUM
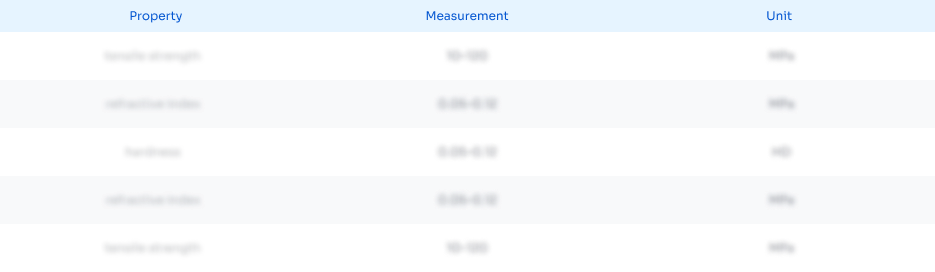
Abstract
Description
Claims
Application Information

- Generate Ideas
- Intellectual Property
- Life Sciences
- Materials
- Tech Scout
- Unparalleled Data Quality
- Higher Quality Content
- 60% Fewer Hallucinations
Browse by: Latest US Patents, China's latest patents, Technical Efficacy Thesaurus, Application Domain, Technology Topic, Popular Technical Reports.
© 2025 PatSnap. All rights reserved.Legal|Privacy policy|Modern Slavery Act Transparency Statement|Sitemap|About US| Contact US: help@patsnap.com