Inner tyre production process and extrusion molding device thereof
A technology of extrusion molding and production process, which is applied in tire processing and manufacturing, powder spraying process in inner tube extrusion molding, and inner tube extrusion molding processing and manufacturing fields, can solve the problems affecting the subsequent use of inner tubes, joint cracking, and affecting quality, etc. Solve the phenomenon of slow air leakage, improve the quality of joints, and solve the effect of bonding problems
- Summary
- Abstract
- Description
- Claims
- Application Information
AI Technical Summary
Problems solved by technology
Method used
Image
Examples
Embodiment Construction
[0026] The present invention is specifically described by the following examples. The examples are only used to further illustrate the present invention, and cannot be interpreted as limiting the protection scope of the present invention. Non-essential improvements and adjustments made by those skilled in the art based on the above-mentioned contents are also acceptable. Belong to the protection scope of the present invention.
[0027] combine Figure 1 to Figure 5 .
[0028] Inner tube production process, including inner tube thermoforming and inner tube joint forming steps, inner tube thermoforming includes thermoforming extrusion, inner powder spraying, cooling, drying, labeling, punching, valve attachment, external powder spraying , fixed-length cutting, and storage process steps. The forming of inner tube tire tube joints includes tire tube confirmation, butt vulcanization, and joint detection steps. The key technology of the present invention is to spray inner powder af...
PUM
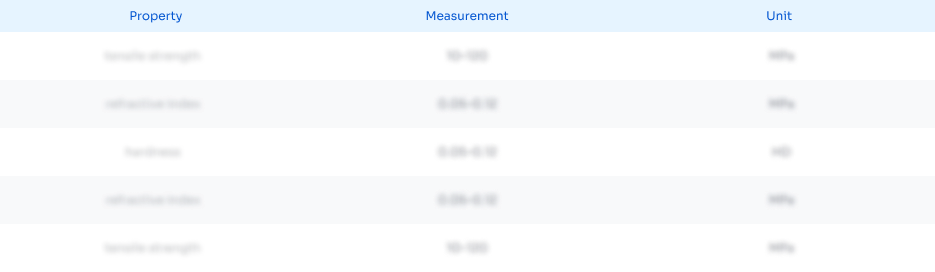
Abstract
Description
Claims
Application Information

- R&D Engineer
- R&D Manager
- IP Professional
- Industry Leading Data Capabilities
- Powerful AI technology
- Patent DNA Extraction
Browse by: Latest US Patents, China's latest patents, Technical Efficacy Thesaurus, Application Domain, Technology Topic, Popular Technical Reports.
© 2024 PatSnap. All rights reserved.Legal|Privacy policy|Modern Slavery Act Transparency Statement|Sitemap|About US| Contact US: help@patsnap.com