Production process of secondary extraction of heparin sodium from enzymatic desorption and adsorption waste liquid
A technology for secondary extraction and production process, applied in the field of production technology for secondary extraction of heparin sodium, can solve the problems of incomplete hydrolysis and adsorption, polluted environment, environmental pollution, etc., and achieves low reaction temperature requirements, low production energy consumption, The effect of high product purity
- Summary
- Abstract
- Description
- Claims
- Application Information
AI Technical Summary
Problems solved by technology
Method used
Examples
Embodiment 1
[0014] ①Flocculation reaction: Take 10 tons of fresh enzyme desorption waste liquid and input it into the reaction tank, add 3wt‰ composite flocculant composed of sodium benzoate, polyvinyl ammonium and pentonite at a ratio of 10:1:1 and 1wt‰toluene , stir the mixed solution at a speed of 100r / min for 5min, add hydrogen chloride to adjust the pH value to 5.5, stir for another 5min, add sodium hydroxide to adjust the pH value to 6.8, stir for 5min, let stand at room temperature for 2 hours, and take out the supernatant for later use. The precipitate is sent to a centrifuge for centrifugation at a centrifugal speed of 5000r / min, the supernatant obtained by centrifugation is mixed with the spare supernatant, and sodium hydroxide is added to adjust the pH value to 10, and the pH value is adjusted again after standing for 2 hours. 7. Leave to settle for 2 hours, take out the standing supernatant and send it to an ultrafilter, and send the sediment obtained by the centrifuge and the ...
Embodiment 2
[0020] ① Flocculation reaction: Take 10 tons of fresh enzyme desorption waste liquid and input it into the reaction tank, add 4wt‰ sodium benzoate, polyvinyl ammonium, potassium alginate, calcium chloride and pentonite according to the ratio of 10:1:1:1:1 Composite flocculant made of components and 1.2wt‰ toluene, stir the mixed solution at a speed of 120r / min for 8 minutes, add sodium hydroxide to adjust the pH value to 6, stir for another 8 minutes, add sodium hydroxide to adjust the pH value to 7.0, and stir for 5 minutes , settling at room temperature for 2.5 hours, pumping out the supernatant for later use, sending the sediment into a centrifuge for centrifugal filtration at a centrifugal speed of 5500r / min, mixing the supernatant obtained by centrifugation with the spare supernatant, and adding hydroxide Adjust the pH value to 10 with sodium, let it settle for 2 hours, adjust the pH value again to 7, let it settle for 2 hours, take out the standing supernatant and send it...
Embodiment 3
[0026] ① Flocculation reaction: Take 10 tons of fresh enzyme desorption waste liquid and input it into the reaction tank, add 5wt‰ of sodium benzoate, polyvinyl ammonium, sodium alginate di-fatty alcohol, alum, perlite crystal powder, barium carbonate and diatom Composite flocculant with 10:0.5:1:1:1:1:1 composition and 1.5wt‰ phenol, stir the mixture at a speed of 150r / min for 10min, add hydrogen chloride to adjust the pH value to 6.5, and then stir 10min, add sodium hydroxide to adjust the pH value to 7.0, stir for 5min, let stand at room temperature for precipitation for 3 hours, take out the supernatant for later use, and send the sediment into a centrifuge for centrifugal filtration at a centrifugal speed of 6000r / min Mix the supernatant with the spare supernatant, add sodium hydroxide to adjust the pH value to 10.5, let it settle for 2 hours, adjust the pH value to 7 again, let it settle for 2 hours, take out the standing supernatant and send it to ultrafiltration machin...
PUM
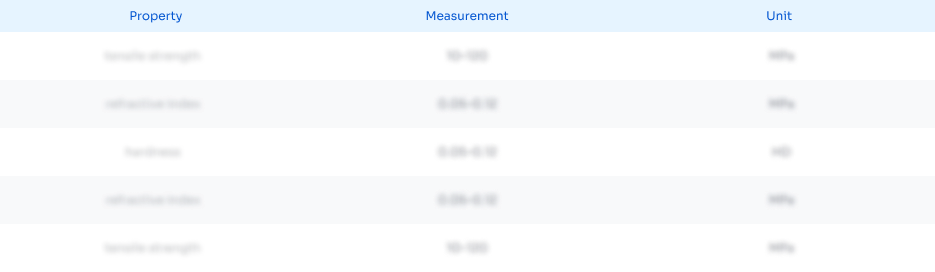
Abstract
Description
Claims
Application Information

- R&D Engineer
- R&D Manager
- IP Professional
- Industry Leading Data Capabilities
- Powerful AI technology
- Patent DNA Extraction
Browse by: Latest US Patents, China's latest patents, Technical Efficacy Thesaurus, Application Domain, Technology Topic, Popular Technical Reports.
© 2024 PatSnap. All rights reserved.Legal|Privacy policy|Modern Slavery Act Transparency Statement|Sitemap|About US| Contact US: help@patsnap.com