Continuous production method of high-efficiency and low-toxicity pesticide-acephate
A kind of acephate, production method technology, is applied in the continuous production field of high-efficiency and low-toxicity insecticide acephate, can solve the disadvantageous large-scale production of acephate, poor production stability and safety, occupying To solve problems such as large land area, to optimize the reaction effect, overcome the effects of large equipment volume and long residence time
- Summary
- Abstract
- Description
- Claims
- Application Information
AI Technical Summary
Problems solved by technology
Method used
Image
Examples
Embodiment 1
[0030] 1. Acylation reaction process
[0031] Control the flow rate of 70% methamidophos to 2000Kg / h, acetic anhydride to 1240Kg / h, catalyst sulfuric acid to 60Kg / h, mix with the solvent dichloromethane, and continuously enter the first-stage acylation reactor, keep at 60°C, stay for 30min and then overflow to II Grade acylation reactor, keep at 70°C, stay for 120min and then enter the neutralization reaction process. Sampling analysis: the content of acephate in the acylation reaction liquid is 54.3%, and the content of methamidophos is <0.05%.
[0032] 2. Neutralization reaction process
[0033] Control the acylation reaction solution to 3300Kg / h, water to 500Kg / h, ammonia gas flow to 250Kg / h, control the neutralization reaction temperature to 35°C, pH=7.5, and enter the extraction process after staying for 30 minutes.
[0034] 3. Extraction process
[0035] Control the neutralization liquid at the bottom of the extraction tower to 4050Kg / h, the flow of chloroform at the ...
Embodiment 2
[0042] 1. Acylation reaction process
[0043] Control the flow rate of 70% methamidophos to 1800Kg / h, acetic anhydride to 1500Kg / h, catalyst phosphoric acid to 60Kg / h, mix with the solvent chloroform, continuously enter the first-stage acylation reactor, keep at 20°C, and overflow to the second-stage acylation reactor after staying for 60 minutes. The reactor was kept at 80°C, and after staying for 180 minutes, it entered the neutralization reaction process. Sampling analysis: the content of acephate in the acylation reaction liquid is 53.5%, and the content of methamidophos is <0.05%.
[0044] 2. Neutralization reaction process
[0045] Control the acylation reaction solution to 3000Kg / h, water to 500Kg / h, ammonia gas flow rate to 250Kg / h, control the neutralization reaction temperature to 10°C, pH=8, and enter the extraction process after staying for 60 minutes.
[0046] 3. Extraction process
[0047] Control the neutralization liquid at the bottom of the extraction tower...
Embodiment 3
[0054] 1. Acylation reaction process
[0055] Control the flow rate of 70% methamidophos to 2000Kg / h, acetic anhydride to 1300Kg / h, catalyst dimethyl sulfate to 60Kg / h, mix with solvent chloroform, and continuously enter the first-stage acylation reactor, keep at 80°C, and overflow to In the second-stage acylation reactor, keep at 80°C, stay for 60 minutes, and then enter the neutralization reaction process. Sampling analysis: the content of acephate in the acylation reaction liquid is 53.8%, and the content of methamidophos is <0.05%.
[0056] 2. Neutralization reaction process
[0057] Control the acylation reaction solution to 3500Kg / h, water to 500Kg / h, ammonia water flow rate to 250Kg / h, control the neutralization reaction temperature to 50°C, pH=7, and enter the extraction process after staying for 5 minutes.
[0058] 3. Extraction process
[0059] Control the neutralization liquid at the bottom of the extraction tower to 4150Kg / h, the flow of chloroform at the top of...
PUM
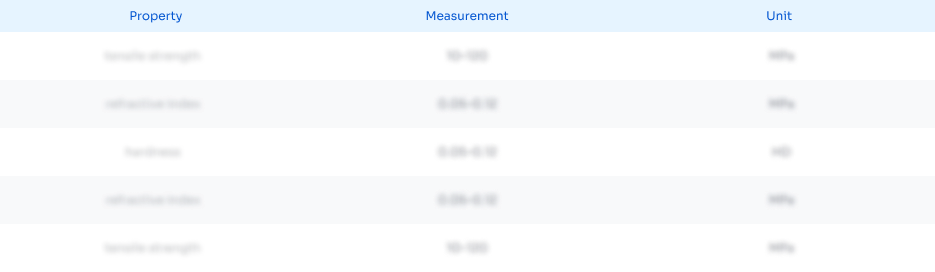
Abstract
Description
Claims
Application Information

- R&D
- Intellectual Property
- Life Sciences
- Materials
- Tech Scout
- Unparalleled Data Quality
- Higher Quality Content
- 60% Fewer Hallucinations
Browse by: Latest US Patents, China's latest patents, Technical Efficacy Thesaurus, Application Domain, Technology Topic, Popular Technical Reports.
© 2025 PatSnap. All rights reserved.Legal|Privacy policy|Modern Slavery Act Transparency Statement|Sitemap|About US| Contact US: help@patsnap.com