Automatic preparation method of long-service-life cylinder-like crystal structural thermal barrier coating on surface of guide blade of hot end part of fuel machine
A technology of hot-end components and columnar crystals, which is applied in the field of long-life thermal barrier coating preparation, and can solve the problems of poor batch stability, low efficiency, and short service life of coatings
- Summary
- Abstract
- Description
- Claims
- Application Information
AI Technical Summary
Problems solved by technology
Method used
Image
Examples
Embodiment Construction
[0025] The technical solution of the present invention will be described in further detail below in conjunction with the accompanying drawings and specific embodiments, but it is not intended as a limitation of the present invention
[0026] (1) Set the tool coordinate tool-HVOF according to the weight, center of gravity, and moment of inertia of the supersonic flame spray gun held by the manipulator, set the distance between the TCP point and the spray gun mouth as 330mm, the moving speed of the spray gun as 500m / s, and the distance between the spraying tracks as 20mm . According to the topography of the hot-end parts to be sprayed, the main program of supersonic flame spraying adhesive layer is compiled. The main program of spraying includes adhesive layer preparation preheating program and adhesive layer preparation program. Time count command.
[0027] (2) Compile the main program of the plasma spraying ceramic layer according to the topography of the hot-end parts to be ...
PUM
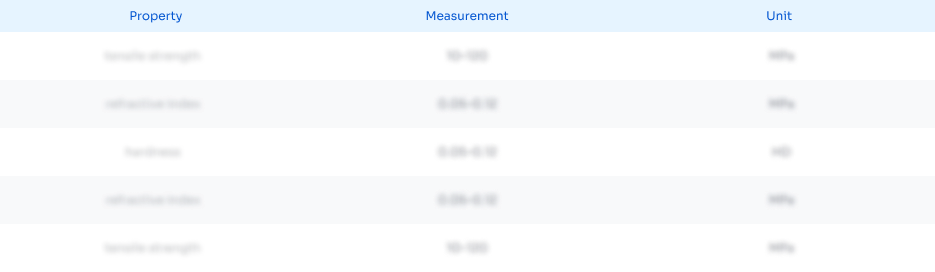
Abstract
Description
Claims
Application Information

- R&D Engineer
- R&D Manager
- IP Professional
- Industry Leading Data Capabilities
- Powerful AI technology
- Patent DNA Extraction
Browse by: Latest US Patents, China's latest patents, Technical Efficacy Thesaurus, Application Domain, Technology Topic, Popular Technical Reports.
© 2024 PatSnap. All rights reserved.Legal|Privacy policy|Modern Slavery Act Transparency Statement|Sitemap|About US| Contact US: help@patsnap.com