Anti-corrosion resin coating and preparation method thereof
An anti-corrosion resin and coating technology, applied in anti-corrosion coatings, epoxy resin coatings, polyamide coatings, etc., can solve the problems of environmental pollution, short anti-corrosion life, thin film, etc. simple effect
- Summary
- Abstract
- Description
- Claims
- Application Information
AI Technical Summary
Problems solved by technology
Method used
Image
Examples
Embodiment 1
[0019] Party:
[0020] Bisphenol F type epoxy resin 20g, polyamide resin 10g, polyurethane 2g, zinc chromate 2g, zinc chloride 1g, mica powder 2g, pigment 1g, talcum powder 2g, acetone 10g, ethanol 10g.
[0021] Preparation:
[0022] (1) Take the polyamide resin and place it in a container, add half of the amount of acetone-ethanol mixed solvent, and disperse at a high speed of 4000r / min for 30 minutes to obtain the primary emulsion;
[0023] (2) Add zinc chromate, zinc chloride, mica powder and pigments to the above-mentioned primary emulsion, and disperse at a high speed of 3600r / min for 20 minutes to obtain a colored slurry;
[0024] (3) Mix bisphenol F epoxy resin and polyurethane, add the remaining mixed solvent, mix with talcum powder and the above-mentioned color paste, disperse at a low speed of 800r / min for 10 minutes, and the product is obtained.
[0025] The polycondensation degree of the bisphenol F type epoxy resin is 30.
Embodiment 2
[0027] Party:
[0028] Bisphenol F type epoxy resin 20g, polyamide resin 20g, polyurethane 10g, zinc chromate 8g, zinc chloride 5g, mica powder 6g, pigment 5g, glass powder 8g, acetone 20g, butanol 20g.
[0029] Preparation:
[0030] (1) Take the polyamide resin and place it in a container, add half of the amount of acetone-butanol mixed solvent, and disperse at a high speed of 6000r / min for 40 minutes to obtain the primary emulsion;
[0031] (2) Add zinc chromate, zinc chloride, mica powder and pigments to the above-mentioned primary emulsion, and disperse at a high speed of 4200r / min for 30 minutes to obtain a colored slurry;
[0032] (3) Mix bisphenol F-type epoxy resin and polyurethane, add the remaining mixed solvent, mix with glass powder and the above-mentioned color paste, disperse at a low speed of 1200r / min for 20 minutes, and the product is obtained.
[0033] The polycondensation degree of the bisphenol F type epoxy resin is 50.
Embodiment 3
[0035] Party:
[0036] Bisphenol F type epoxy resin 20g, polyamide resin 15g, polyurethane 6g, zinc chromate 5g, zinc chloride 3g, mica powder 4g, pigment 3g, diatomaceous earth 5g, acetone 10g, ethanol 10g, xylene 10g.
[0037] Preparation:
[0038] (1) Take the polyamide resin and place it in a container, add half of the amount of acetone-ethanol-xylene mixed solvent, and disperse at a high speed of 5000r / min for 35 minutes to obtain the primary emulsion;
[0039] (2) Add zinc chromate, zinc chloride, mica powder and pigments to the above-mentioned primary emulsion, and disperse at a high speed of 3900r / min for 25 minutes to obtain a colored paste;
[0040] (3) Mix bisphenol F-type epoxy resin and polyurethane, add the remaining mixed solvent, mix with diatomaceous earth and the above-mentioned color paste, disperse at a low speed of 1000r / min for 15 minutes, and the product is obtained.
[0041] The polycondensation degree of the bisphenol F type epoxy resin is 40.
PUM
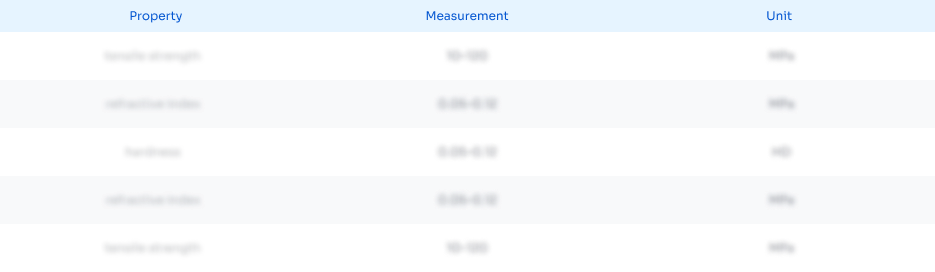
Abstract
Description
Claims
Application Information

- R&D
- Intellectual Property
- Life Sciences
- Materials
- Tech Scout
- Unparalleled Data Quality
- Higher Quality Content
- 60% Fewer Hallucinations
Browse by: Latest US Patents, China's latest patents, Technical Efficacy Thesaurus, Application Domain, Technology Topic, Popular Technical Reports.
© 2025 PatSnap. All rights reserved.Legal|Privacy policy|Modern Slavery Act Transparency Statement|Sitemap|About US| Contact US: help@patsnap.com