Solution-curing quick-molding manufacturing method
A manufacturing method and curing molding technology, applied in the field of solution curing rapid prototyping manufacturing, can solve the problems of insufficient additive manufacturing technology, complex equipment structure, high control difficulty, rich production methods, simple equipment form, and expanded raw material range. Effect
- Summary
- Abstract
- Description
- Claims
- Application Information
AI Technical Summary
Problems solved by technology
Method used
Image
Examples
Embodiment 1
[0024] Embodiment 1, as shown in the figure, the solution curing rapid prototyping manufacturing method of this embodiment includes steps:
[0025] (1) Prepare the solution raw material as the printing raw material, and put the solution raw material into the storage container 1 to maintain its stability and uniformity;
[0026] (2) Utilize computer 2 to carry out program cutting and layering to the product to be formed, form each virtual layer that forms product, utilize program cutting and layering product to belong to prior art, can utilize existing cad design software to finish;
[0027] (3) Adopt the pump 3 to spray the solution raw material in the storage container 1 into the coagulation bath 5 through the print nozzle 4, the coagulation bath 5 is provided with a liftable workbench 7 carrying the product 6, and the pump 3 is controlled by the computer 2 The starting and stopping, the flow rate of the pump and the movement trajectory of the printing nozzle make the raw mat...
Embodiment 2
[0035] Embodiment 2: The difference between the solution solidification rapid prototyping manufacturing method of this embodiment and Embodiment 1 is that: in step (3), the solution raw material undergoes a chemical reaction during contact with the coagulation bath to solidify and form, and the solution raw material It is an epoxy resin emulsion, and the coagulation bath is water, water vapor, air or nitrogen; certainly in different embodiments, the raw material of the solution can also be cement mortar, and the coagulation bath is water, water vapor, air or nitrogen. Nitrogen: The solution raw material can also be anaerobic glue, and the coagulation bath includes water, water vapor, air or nitrogen. Other steps of the solution curing rapid prototyping manufacturing method in this embodiment are the same as those in Embodiment 1, and will not be repeated here.
Embodiment 3
[0036] Embodiment three: the difference between the solution solidification rapid prototyping manufacturing method of this embodiment and embodiment one is that: in step (3), the solution raw material undergoes a crystallization reaction during contact with the coagulation bath to solidify and form, and the solution raw material Including lignocellulose emulsion, the coagulation bath is water; of course, in different embodiments, the solution raw material can also be chitosan solution, and the coagulation bath is water. Other steps of the solution curing rapid prototyping manufacturing method in this embodiment are the same as those in Embodiment 1, and will not be repeated here.
PUM
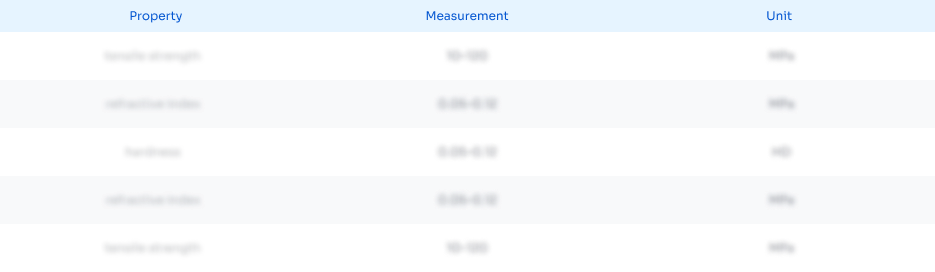
Abstract
Description
Claims
Application Information

- R&D Engineer
- R&D Manager
- IP Professional
- Industry Leading Data Capabilities
- Powerful AI technology
- Patent DNA Extraction
Browse by: Latest US Patents, China's latest patents, Technical Efficacy Thesaurus, Application Domain, Technology Topic, Popular Technical Reports.
© 2024 PatSnap. All rights reserved.Legal|Privacy policy|Modern Slavery Act Transparency Statement|Sitemap|About US| Contact US: help@patsnap.com