Aluminum alloy for microporous hollow material which has excellent extrudability and grain boundary corrosion resistance, and method for producing same
A manufacturing method, corrosion-resistant technology, applied in the field of aluminum alloys, can solve the problems of heat exchanger performance reduction, Zn concentration increase in Zn diffusion layer, and insufficient realization of solutions, etc., to achieve good extrudability and grain boundary corrosion resistance excellent effect
- Summary
- Abstract
- Description
- Claims
- Application Information
AI Technical Summary
Problems solved by technology
Method used
Image
Examples
Embodiment
[0074] As the fluid for heat exchange, a Freon-based refrigerant is used. Therefore, as a raw material used for heat exchangers, it is necessary to be excellent in corrosion resistance, strength, and brazability, and to be able to manufacture micropore hollow profiles (flat tubes) of about 0.5 to 2 mm as main parts of heat exchanger assemblies. Alloys for extrusion processing.
[0075] Here, for various aluminum alloys having the chemical compositions shown in Table 1, extrusion formability, corrosion resistance, strength, and brazability were verified.
[0076] First, various aluminum alloys having chemical compositions shown in Table 1 were melted to produce cast bodies (billets) with a diameter of 6 to 10 inches and a length of 2 to 6 m. The billet is kept at 550-590°C for 0.5-6 hours to perform homogenization treatment, after that, it is heated to 460-550°C, and extruded with a thin-walled profile mold with an extrusion ratio of 30-1000. Figure 4 A hollow flat tube 1 fo...
PUM
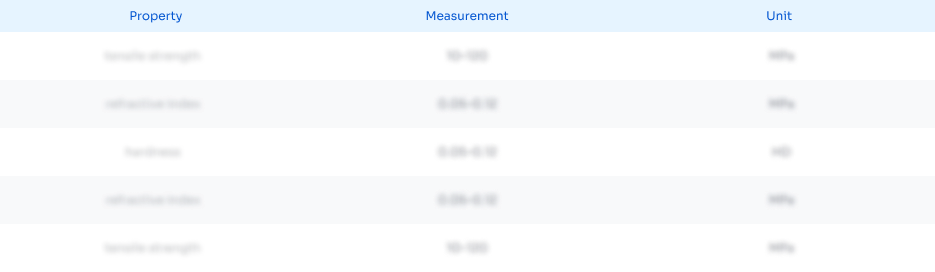
Abstract
Description
Claims
Application Information

- R&D
- Intellectual Property
- Life Sciences
- Materials
- Tech Scout
- Unparalleled Data Quality
- Higher Quality Content
- 60% Fewer Hallucinations
Browse by: Latest US Patents, China's latest patents, Technical Efficacy Thesaurus, Application Domain, Technology Topic, Popular Technical Reports.
© 2025 PatSnap. All rights reserved.Legal|Privacy policy|Modern Slavery Act Transparency Statement|Sitemap|About US| Contact US: help@patsnap.com