Anticorrosive coating method for electric locomotive
A technology for electric locomotives and a coating method, which is applied to devices for coating liquid on surfaces, coatings, etc., can solve problems such as failure to meet environmental protection requirements, slow drying of asphalt coatings, and easy damage to paints, and achieves good spray construction. , long-term decorative performance, excellent matching effect
- Summary
- Abstract
- Description
- Claims
- Application Information
AI Technical Summary
Problems solved by technology
Method used
Image
Examples
Embodiment Construction
[0016] Such as Figure 1-3 As shown, the embodiment of the present invention provides a kind of electric locomotive anticorrosion coating method, and this method comprises the following steps:
[0017] Step 1), perform mechanical pretreatment on the overall surface of the electric locomotive: including the inner surface of the car body, the outer surface of the car body, the inner surface of the driver, the outer surface of the driver, the surface of the chassis and the surface of the bogie, all surfaces to be painted;
[0018] Step 2), spraying a primer of heavy-duty anti-corrosion paint on the outer surface of the electric locomotive car body, the outer surface of the cab, the surface of the chassis and the surface of the bogie to form a primer layer 1, the thickness of the primer layer 1 is between 80 and 100 μm;
[0019] Step 3), spraying the bottom-surface-integrated paint of the heavy-duty anti-corrosion coating on the surface of the cab of the electric locomotive and th...
PUM
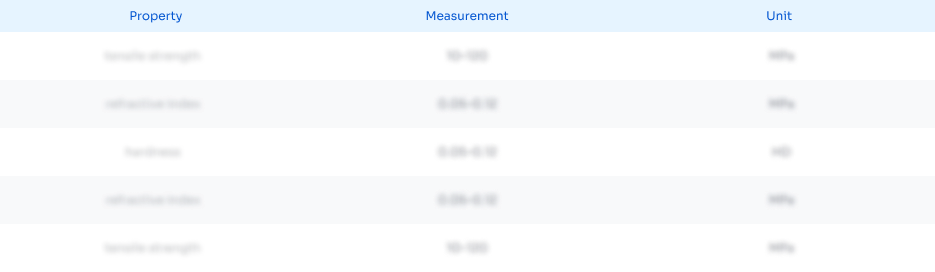
Abstract
Description
Claims
Application Information

- Generate Ideas
- Intellectual Property
- Life Sciences
- Materials
- Tech Scout
- Unparalleled Data Quality
- Higher Quality Content
- 60% Fewer Hallucinations
Browse by: Latest US Patents, China's latest patents, Technical Efficacy Thesaurus, Application Domain, Technology Topic, Popular Technical Reports.
© 2025 PatSnap. All rights reserved.Legal|Privacy policy|Modern Slavery Act Transparency Statement|Sitemap|About US| Contact US: help@patsnap.com