Vacuum furnace quenching process
A vacuum furnace and process technology, which is applied in the field of vacuum furnace quenching process, can solve the problems of slow quenching speed, oxygen content in the atmosphere, and increased production costs, and achieve flexible production mobilization, deep hardening depth and hardness uniformity, and cost reduction. Effect
- Summary
- Abstract
- Description
- Claims
- Application Information
AI Technical Summary
Problems solved by technology
Method used
Image
Examples
Embodiment Construction
[0013] In this example, refer to figure 1 As shown, a vacuum furnace quenching process includes a quenching pool 3 and a precooling chamber 2, and a heating chamber 1 connected to the precooling chamber 2; a heating device 10 is arranged in the heating chamber 1; the heating chamber 1 and the An insulated door 4 is arranged between the pre-cooling chambers 2; the quenching pool 3 is connected to a preparatory warehouse 5, and a quenching liquid discharge copper pipe 61 and a quenching liquid return copper pipe are arranged between the quenching pool 3 and the preparatory warehouse 5 62; the quenching liquid discharge copper pipe 61 and the quenching liquid return copper pipe 62 are respectively provided with a liquid discharge pump 71 and a liquid return pump 72; a baffle valve is provided between the liquid discharge pump 71 and the quenching pool 3 8; a baffle valve 8 is also provided between the liquid return pump 72 and the quenching pool 3; a filter 9 is provided between ...
PUM
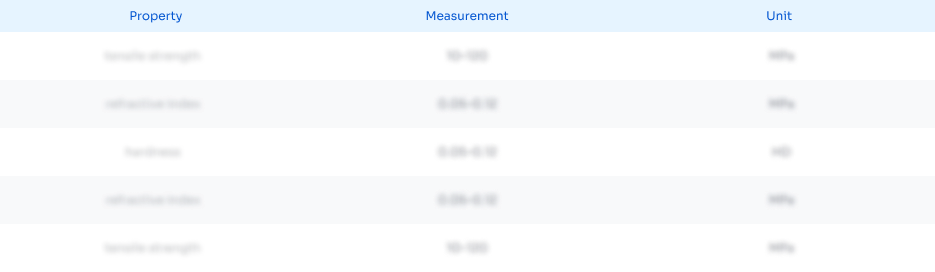
Abstract
Description
Claims
Application Information

- R&D
- Intellectual Property
- Life Sciences
- Materials
- Tech Scout
- Unparalleled Data Quality
- Higher Quality Content
- 60% Fewer Hallucinations
Browse by: Latest US Patents, China's latest patents, Technical Efficacy Thesaurus, Application Domain, Technology Topic, Popular Technical Reports.
© 2025 PatSnap. All rights reserved.Legal|Privacy policy|Modern Slavery Act Transparency Statement|Sitemap|About US| Contact US: help@patsnap.com