Composite damping material
A technology of composite damping material and parts by weight, which is applied in the field of composite damping materials, can solve the problems of unsatisfactory sound wave energy attenuation effect, inability to effectively stagger the anastomotic valley effect, etc., and achieve outstanding noise reduction performance, wide damping temperature range, and low The effect of wide noise band
- Summary
- Abstract
- Description
- Claims
- Application Information
AI Technical Summary
Problems solved by technology
Method used
Examples
Embodiment 1
[0008] A composite damping material comprising the following parts by weight: 60 parts of isoprene rubber, 46 parts of emulsion polystyrene butadiene rubber, 14 parts of N-phenyl-β-naphthylamine, 6-ethoxy-2,2, 10 parts of 4-trimethyl-1,2-dihydroquinoline, 13 parts of stannous octoate, 4 parts of cobalt naphthenate, 7 parts of N,N-diethylaniline, 14 parts of benzoyl peroxide, sulfur 7 parts, 17 parts of chlorinated paraffin, 45 parts of isopropanol, 70 parts of calcium carbonate, 17 parts of carbon black, 9 parts of zinc stearate, 32 parts of polyisobutylene.
Embodiment
[0010] A composite damping material comprising the following parts by weight: 25 parts of isoprene rubber, 35 parts of emulsion polystyrene butadiene rubber, 10 parts of N-phenyl-β-naphthylamine, 6-ethoxy-2,2, 5 parts of 4-trimethyl-1,2-dihydroquinoline, 10 parts of stannous octoate, 3 parts of cobalt naphthenate, 1 part of N,N-diethylaniline, 14 parts of benzoyl peroxide, sulfur 4 parts, 5 parts of chlorinated paraffin, 30 parts of isopropanol, 45 parts of calcium carbonate, 10 parts of carbon black, 3 parts of zinc stearate, 15 parts of polyisobutylene.
PUM
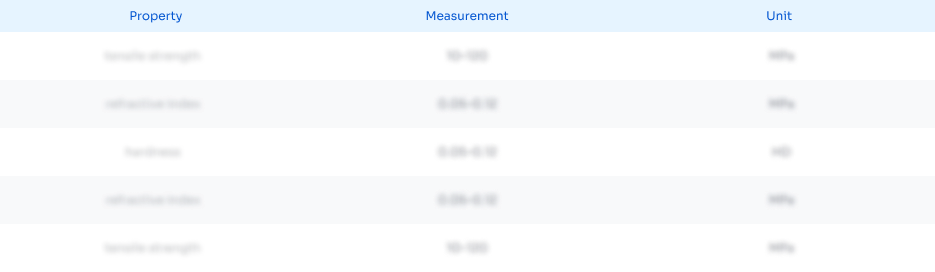
Abstract
Description
Claims
Application Information

- R&D Engineer
- R&D Manager
- IP Professional
- Industry Leading Data Capabilities
- Powerful AI technology
- Patent DNA Extraction
Browse by: Latest US Patents, China's latest patents, Technical Efficacy Thesaurus, Application Domain, Technology Topic, Popular Technical Reports.
© 2024 PatSnap. All rights reserved.Legal|Privacy policy|Modern Slavery Act Transparency Statement|Sitemap|About US| Contact US: help@patsnap.com