High-efficiency and energy-saving new lean magnetite combined milling magnetic separation method
A high-efficiency and energy-saving technology for magnetite ore, applied in chemical instruments and methods, magnetic separation, solid separation, etc., can solve the problems of large consumption of steel balls and liners, high energy consumption of process operations, and high comprehensive cost of beneficiation. The effect of reducing power consumption, reducing model and installed power, reducing specifications and installed power
- Summary
- Abstract
- Description
- Claims
- Application Information
AI Technical Summary
Problems solved by technology
Method used
Image
Examples
Embodiment Construction
[0030] In order to describe the present invention, a new method of combined crushing, grinding and magnetic separation of magnetite ore with high efficiency and energy saving according to the present invention will be further described in detail in conjunction with the accompanying drawings and examples.
[0031] The ore sample in the example of the present invention is taken from the core sample of Zhangzhuang Iron Mine of Maanshan Iron and Steel Co., Ltd., and the raw ore iron grade is 29.56%, which belongs to typical lean magnetite. For this ore sample, by figure 1 The principle process flow chart of a kind of efficient and energy-saving magnetite-lean combined crushing and grinding magnetic separation new method of the present invention shown and combined figure 2 It can be seen that a kind of high-efficiency and energy-saving lean magnetite ore of the present invention combined crushing and grinding magnetic separation new method adopts specific technique, step:
[0032...
PUM
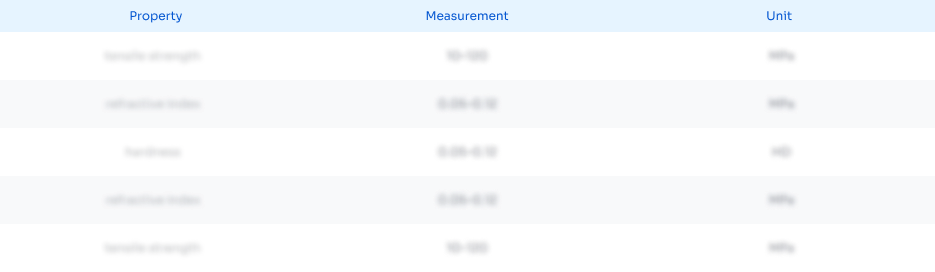
Abstract
Description
Claims
Application Information

- Generate Ideas
- Intellectual Property
- Life Sciences
- Materials
- Tech Scout
- Unparalleled Data Quality
- Higher Quality Content
- 60% Fewer Hallucinations
Browse by: Latest US Patents, China's latest patents, Technical Efficacy Thesaurus, Application Domain, Technology Topic, Popular Technical Reports.
© 2025 PatSnap. All rights reserved.Legal|Privacy policy|Modern Slavery Act Transparency Statement|Sitemap|About US| Contact US: help@patsnap.com