Micro-pore polishing equipment and micro-pore polishing process for abrasive particle flow
An abrasive flow and microporous technology, applied in the field of abrasive flow microporous polishing process and abrasive particle flow microporous polishing equipment, can solve the problems of hydraulic components and pipeline requirements, difficulties, unsafe equipment systems, etc.
- Summary
- Abstract
- Description
- Claims
- Application Information
AI Technical Summary
Problems solved by technology
Method used
Image
Examples
Embodiment Construction
[0022] Embodiments of the present invention are described in detail below.
[0023] Such as figure 1 , figure 2 As shown, the present invention is an abrasive particle flow microhole polishing device, which includes a fixture 12 for clamping a workpiece 10 and positioning the microholes 11 to be polished in the workpiece 10, a base plate 15 installed on the fixture 12, The through-hole-shaped cavitation cavity 16 that is located on the base plate 15 and communicates with the microhole 11 of the workpiece 10, and the laser high-transparency protective mirror 18 that covers the side of the cavitation cavity 16 opposite to the workpiece 10 can produce The laser for the laser beam 22 towards the cavitation cavity 16, the focusing lens 20 that can focus the laser beam 22 in the cavitation cavity 16 between the laser and the laser high-transparency protective mirror 18, and the pressure abrasive fluid Abrasive guide channels 24 leading into the cavitation cavity 16 . The abrasiv...
PUM
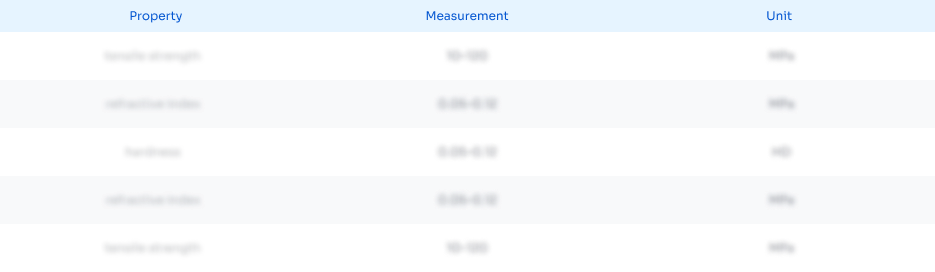
Abstract
Description
Claims
Application Information

- R&D
- Intellectual Property
- Life Sciences
- Materials
- Tech Scout
- Unparalleled Data Quality
- Higher Quality Content
- 60% Fewer Hallucinations
Browse by: Latest US Patents, China's latest patents, Technical Efficacy Thesaurus, Application Domain, Technology Topic, Popular Technical Reports.
© 2025 PatSnap. All rights reserved.Legal|Privacy policy|Modern Slavery Act Transparency Statement|Sitemap|About US| Contact US: help@patsnap.com