Utilization method of waste heat from ferronickel smelting in rkef process
A nickel-iron and process technology, applied in the field of comprehensive utilization of waste heat in ferroalloy production, can solve the problems of large coal or metallurgical coke and electric energy consumption, large amount of slag in the smelting process, large energy consumption, etc., to reduce carbon "emission" and "sulfur" Emissions, obvious economic and social benefits, and the effect of saving the amount of pulverized coal
- Summary
- Abstract
- Description
- Claims
- Application Information
AI Technical Summary
Problems solved by technology
Method used
Image
Examples
Embodiment 1
[0023] A factory adopts RKEF process to produce ferronickel, the high temperature flue gas of electric furnace is 950℃, and the flue gas volume is 24370Nm 3 / h, the temperature is lowered to 750°C by mixing air in the air mixing chamber, and the flue gas volume becomes 29134Nm 3 / h, 400°C hot air is generated after heat exchange, and the air volume is 51048Nm 3 / h, hot air used as the secondary air for coal injection combustion in the rotary kiln can save 5942 tons of coal consumption per year; the flue gas temperature of the rotary kiln is 300 °C, and the flue gas volume is 90239Nm 3 / h, after the dust is collected by the cyclone dust collector, the temperature of the flue gas is reduced to 250°C, and then blown into the mixing chamber of the drying kiln by a high-temperature fan as a heat source for the drying kiln, which can save 6,297 tons of coal consumption per year. The two waste heat utilization can reduce "carbon" emission by 7904 tons and "sulfur" emission by 98 ton...
Embodiment 2
[0025] A factory adopts RKEF process to produce ferronickel, the high temperature flue gas of electric furnace is 1000℃, and the flue gas volume is 22628Nm 3 / h, the temperature is lowered to 750°C through the mixed air in the air mixing chamber, and the flue gas volume becomes 28158Nm 3 / h, 400°C hot air is generated after heat exchange, and the air volume is 49322Nm 3 / h, the hot air used as the secondary air for coal injection combustion in the rotary kiln can save 5,741 tons of coal consumption per year; the flue gas temperature of the rotary kiln is 350°C, and the flue gas volume is 88,235Nm 3 / h, after the dust is collected by the cyclone dust collector, the temperature of the flue gas is reduced to 300°C, and then blown into the mixing chamber of the drying kiln by a high-temperature fan as a heat source for the drying kiln, which can save 6,442 tons of coal consumption per year. The two waste heat utilization can reduce "carbon" emissions by 7868 tons and "sulfur" emi...
PUM
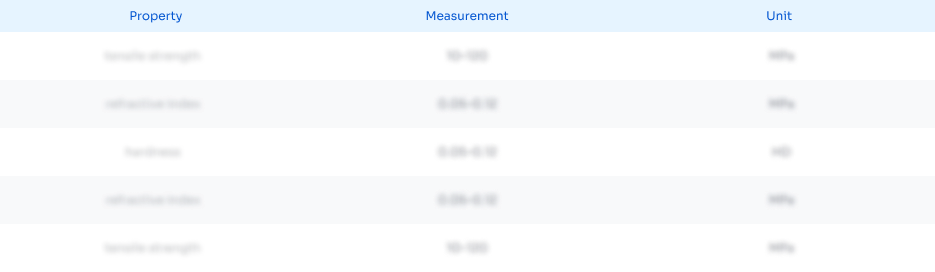
Abstract
Description
Claims
Application Information

- R&D Engineer
- R&D Manager
- IP Professional
- Industry Leading Data Capabilities
- Powerful AI technology
- Patent DNA Extraction
Browse by: Latest US Patents, China's latest patents, Technical Efficacy Thesaurus, Application Domain, Technology Topic, Popular Technical Reports.
© 2024 PatSnap. All rights reserved.Legal|Privacy policy|Modern Slavery Act Transparency Statement|Sitemap|About US| Contact US: help@patsnap.com