High-temperature-edible-oil-resistant silicone rubber blend and preparation method thereof
A technology of silicone rubber and edible oil, which is applied in the field of high temperature resistant edible oil silicone rubber blends and its preparation, can solve the problems of poor compatibility and damage to the mechanical properties of silicone rubber, and achieve low cost, good dimensional stability, The effect of small change in mechanical properties
- Summary
- Abstract
- Description
- Claims
- Application Information
AI Technical Summary
Problems solved by technology
Method used
Image
Examples
Embodiment 2
[0030] In parts by mass, the consumption of each raw material is as follows:
[0031]
[0032] at 6.5 x 10 4Under Pa, use the vacuum ultraviolet radiation source generated by helium plasma to carry out photoetching treatment on the surface of PTFE micropowder for 8 minutes, and expose the etched PTFE micropowder in the atmosphere for more than 10 minutes to obtain surface modified PTFE micropowder. Put methyl vinyl silicone rubber, fumed silica, and hydroxy silicone oil (viscosity 5Pa·s) into the open mill and mix evenly, then add surface-modified PTFE micropowder into the open mill in batches, adjust the roller distance to 1mm, thin Pass 5 times to make it evenly dispersed, and finally add the vulcanizing agent di-tert-butyl peroxide hexane, and mix evenly. The total mixing time is 30 minutes, and the temperature of the roller is controlled below 45°C. Parked for 12 hours, back to practice. The vulcanization condition of the silicone rubber blend is 180°C x 5 minutes, an...
Embodiment 3
[0034] In parts by mass, the consumption of each raw material is as follows:
[0035]
[0036]
[0037] at 6.5 x 10 4 Under Pa, use a vacuum ultraviolet radiation source generated by helium plasma to carry out surface photoetching treatment on the PTFE micropowder for 10 minutes, and expose the etched PTFE micropowder to the atmosphere for more than 10 minutes to obtain a surface-modified PTFE micropowder. Put methyl vinyl silicone rubber, fumed silica, and hydroxyl silicone oil (viscosity 0.5Pa·s) into the open mill and mix evenly, then add surface-modified PTFE micropowder into the open mill in batches, adjust the roller distance to 1mm, Thin pass 8 times to make it uniformly dispersed, and finally add the vulcanizing agent di-tert-butyl peroxide hexane, mix evenly, the total mixing time is 30 minutes, and control the temperature of the rollers below 45°C. Parked for 12 hours, back to practice. The vulcanization condition of the silicone rubber blend is 180°C x 5 min...
Embodiment 4
[0040] In parts by mass, the consumption of each raw material is as follows:
[0041]
[0042] at 6.5 x 10 4 Under Pa, use the vacuum ultraviolet radiation source generated by helium plasma to carry out photoetching treatment on the surface of PTFE micropowder for 8 minutes, and expose the etched PTFE micropowder in the atmosphere for more than 10 minutes to obtain surface modified PTFE micropowder. Put methyl vinyl silicone rubber, fumed silica, and hydroxyl silicone oil (viscosity 0.5Pa·s) into the open mill and mix evenly, then add surface-modified PTFE micropowder into the open mill in batches, adjust the roller distance to 1mm, Thin pass 8 times to make it uniformly dispersed, and finally add the vulcanizing agent di-tert-butyl peroxide hexane, mix evenly, the total mixing time is 30 minutes, and control the temperature of the rollers below 45°C. Parked for 12 hours, back to practice. The vulcanization condition of the silicone rubber blend is 180°C x 5 minutes, and ...
PUM
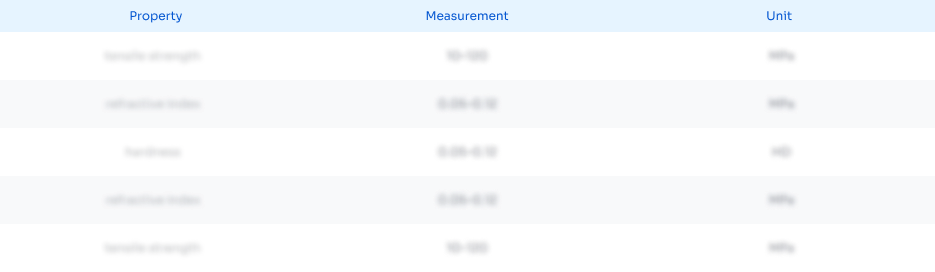
Abstract
Description
Claims
Application Information

- R&D Engineer
- R&D Manager
- IP Professional
- Industry Leading Data Capabilities
- Powerful AI technology
- Patent DNA Extraction
Browse by: Latest US Patents, China's latest patents, Technical Efficacy Thesaurus, Application Domain, Technology Topic, Popular Technical Reports.
© 2024 PatSnap. All rights reserved.Legal|Privacy policy|Modern Slavery Act Transparency Statement|Sitemap|About US| Contact US: help@patsnap.com