Method for extremely fine grinding and finishing surface of cam of internal combustion engine camshaft through electrochemical composite oilstone with reverse pulses
A cam surface and reverse pulse technology is applied in the field of finishing of the cam surface of an internal combustion engine.
- Summary
- Abstract
- Description
- Claims
- Application Information
AI Technical Summary
Problems solved by technology
Method used
Image
Examples
Embodiment Construction
[0014] The present invention will be further described below in conjunction with the accompanying drawings and specific embodiments.
[0015] Such as figure 1 As shown, the electrochemical compound oil stone superfinishing finishing device with reverse pulse on the entire internal combustion engine cam surface is composed of the camshaft rotary motion system, the electrode motion system and the oil stone motion system.
[0016] The camshaft 1 is driven by the servo motor to rotate at a constant speed, the speed is 120r / min, and the camshaft is connected to one pole of the power supply;
[0017] The electrode 2 is placed on the CNC table 3, and the servo motor drives the CNC table 3 to move back and forth, thereby driving the electrode 2 to move back and forth, and maintain a constant gap with the cam, the gap value is 5mm, and the electrode is connected to the other pole of the power supply;
[0018] A neutral electrolyte 4 is passed between the cam 1 and the electrode 2,...
PUM
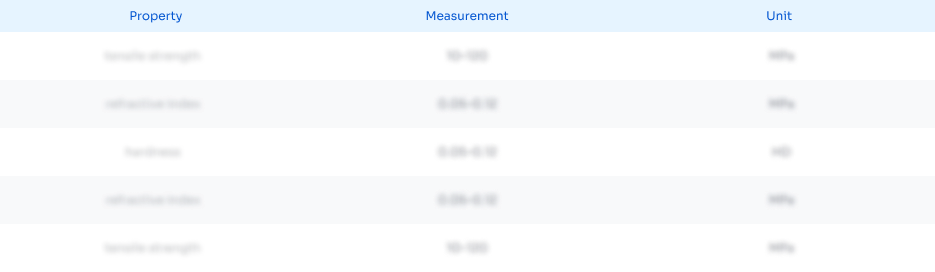
Abstract
Description
Claims
Application Information

- R&D
- Intellectual Property
- Life Sciences
- Materials
- Tech Scout
- Unparalleled Data Quality
- Higher Quality Content
- 60% Fewer Hallucinations
Browse by: Latest US Patents, China's latest patents, Technical Efficacy Thesaurus, Application Domain, Technology Topic, Popular Technical Reports.
© 2025 PatSnap. All rights reserved.Legal|Privacy policy|Modern Slavery Act Transparency Statement|Sitemap|About US| Contact US: help@patsnap.com