Knotting process for permanent layer of small and medium-sized refining ladle
A process method and permanent layer technology, applied in the direction of manufacturing tools, metal processing equipment, casting melt containers, etc., can solve the problems of poor knotting effect of the permanent layer, inconvenient mold preparation and practical operation, etc., and achieve good masonry quality. , the effect of saving turnover, practicality and wide applicability
- Summary
- Abstract
- Description
- Claims
- Application Information
AI Technical Summary
Problems solved by technology
Method used
Examples
Embodiment Construction
[0014] The process steps are as follows:
[0015] Step 1: Lay a layer of 20 mm thick insulation board on the bottom of the ladle;
[0016] Step 2: Knot the permanent layer of the bottom of the bag and keep it healthy for 24 hours;
[0017] Step 3: After the bottom of the bag is completely solidified, lay the bottom bricks; paste the first layer of insulation board on the wall along the bottom of the bag, and build the first layer of working bricks, leaving a gap of 75-90 mm in the middle;
[0018] Step 4: Fill the gap between the wall brick and the heat insulation layer with water and a good aluminum-magnesium spinel castable. The proportion of water is 6-7%. Use a vibrating rod to vibrate;
[0019] Step 5: Paste the second layer of insulation board on the wall, build the second layer of working bricks, pour the second layer of castable and compact, and then build layer by layer;
[0020] Step 6: Keep in good health for 12 hours; first bake on low fire for 4 hours, then bake on high fire...
PUM
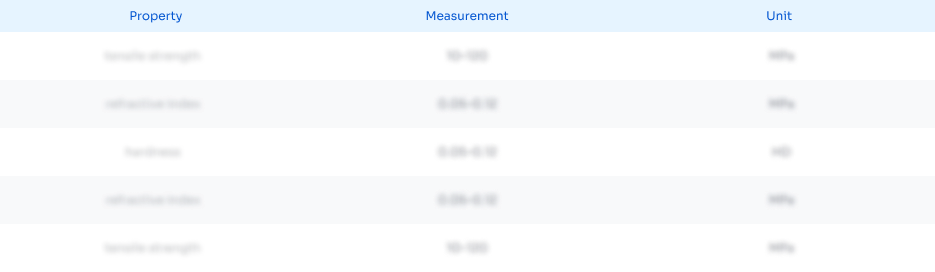
Abstract
Description
Claims
Application Information

- R&D
- Intellectual Property
- Life Sciences
- Materials
- Tech Scout
- Unparalleled Data Quality
- Higher Quality Content
- 60% Fewer Hallucinations
Browse by: Latest US Patents, China's latest patents, Technical Efficacy Thesaurus, Application Domain, Technology Topic, Popular Technical Reports.
© 2025 PatSnap. All rights reserved.Legal|Privacy policy|Modern Slavery Act Transparency Statement|Sitemap|About US| Contact US: help@patsnap.com