Sintering apparatus
A technology of sintering device and furnace core tube, which is applied in glass forming, lighting and heating equipment, furnace components, etc., and can solve problems such as leakage
- Summary
- Abstract
- Description
- Claims
- Application Information
AI Technical Summary
Problems solved by technology
Method used
Image
Examples
Embodiment 1
[0023] figure 2 It is a schematic diagram of the structure near the cover 4 used in Example 1. Such as figure 2 As shown, a protrusion 10 is provided near the upper end of the inner wall of the furnace core tube 3 , and an inner cover 11 supported by the protrusion is provided to divide the upper end region of the furnace core tube 3 into two. The gap between the inner cover 11 and the furnace core tube 3 is 0.5 mm, and the gap between the inner cover 11 and the shaft body 7 on which the soot deposit body 8 hangs down is 1 mm. These gaps form a gas flow path that communicates with the upper and lower halves of the inner cover 11, and does not completely block the flow of atmospheric gas. When the soot deposited body 8 was sintered in the same manner as in the comparative example with such a structure, it was found that no minute air bubbles as seen in the comparative example remained in the obtained glass body.
[0024] It can be seen that by making the sum of the cross-s...
Embodiment 2
[0027] image 3 It is a schematic diagram of the structure near the cover 4 used in Example 2. Such as image 3 As shown, a step 12 is provided near the upper end of the inner wall of the furnace core tube 3, and an inner cover 11 supported by the step 12 is provided to divide the upper end area of the furnace core tube 3 into two along the upper and lower sides. The gap between the inner cover 11 and the shaft body 7 on which the soot deposit body 8 hangs down is 1 mm. This gap forms a gas flow path connecting the upper and lower halves of the inner cover 11, and does not completely block the flow of atmospheric gas. When the soot deposited body 8 was sintered in the same manner as in the comparative example with this structure, it was found that no minute air bubbles as seen in the comparative example remained in the obtained glass body.
PUM
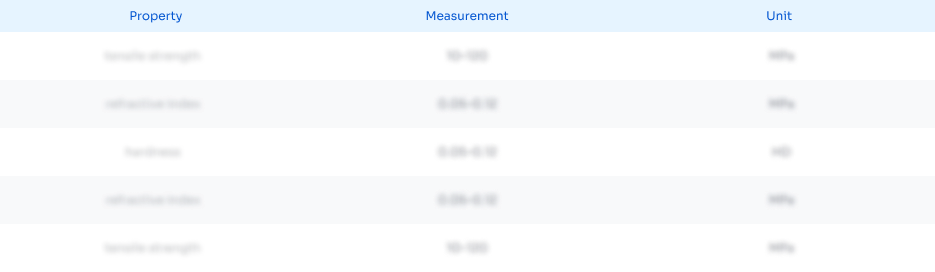
Abstract
Description
Claims
Application Information

- R&D
- Intellectual Property
- Life Sciences
- Materials
- Tech Scout
- Unparalleled Data Quality
- Higher Quality Content
- 60% Fewer Hallucinations
Browse by: Latest US Patents, China's latest patents, Technical Efficacy Thesaurus, Application Domain, Technology Topic, Popular Technical Reports.
© 2025 PatSnap. All rights reserved.Legal|Privacy policy|Modern Slavery Act Transparency Statement|Sitemap|About US| Contact US: help@patsnap.com