Bamboo floor preparation process
A preparation process, bamboo floor technology, applied in the direction of manufacturing tools, wood processing appliances, wooden veneer joints, etc., can solve the problems of bamboo floor life and loss of physical properties, achieve good strength and hardness, compact preparation process, Guarantee the effect of processing quality
- Summary
- Abstract
- Description
- Claims
- Application Information
AI Technical Summary
Problems solved by technology
Method used
Examples
Embodiment 1
[0026] This kind bamboo floor preparation technology comprises the steps:
[0027] 1) material preparation: cut off the procured raw bamboo and slice into bamboo slices of the same size;
[0028] 2) Rough milling: flatten the bamboo joints, and remove the green and yellow parts of the bamboo slices by milling;
[0029] 3) Cooking and carbonization: remove the sugar and fat in the bamboo chips, and enhance the hardness and strength of the bamboo chips;
[0030] 4) drying: drying the bamboo chips to a moisture content of <7%;
[0031] 5) manual selection: select the bamboo chips that meet the splicing conditions;
[0032] 6) fine milling: milling the bamboo green and bamboo yellow of the dried bamboo chips;
[0033] 7) Stitching and pressing: using a hot press to hot-press and glue multiple pieces of bamboo to form a bamboo blank;
[0034] 8) planing: planing the bamboo slabs to make the surface smooth;
[0035] 9) Grooving on all sides: use a slotting machine to slot the b...
Embodiment 2
[0043] The difference between the present embodiment and the first embodiment is: in the present embodiment, in step 3), the temperature of the primary carbonization is controlled at 140° C., and the time is 2 hours. After the bamboo chips after the primary carbonization are completely cooled, carry out Secondary carbonization: carbonize the bamboo chips at a high temperature of 125°C for 2 hours, and then raise the temperature to 135°C for 1 hour. During the secondary carbonization process of the present embodiment, the humidity is maintained at 85%;
[0044] In addition, the hot-pressing temperature in step 7) is 150° C., the hot-pressing pressure is 1.0 MPa, and the hot-pressing time is 15 minutes.
Embodiment 3
[0046] The difference between this embodiment and Embodiment 1 is that in this embodiment, the temperature of the primary carbonization is controlled at 130°C for 2.5 hours, and after the bamboo chips after the primary carbonization are completely cooled, the secondary carbonization is carried out. Carbonization First carbonize the bamboo chips at a high temperature of 120°C for 2.2 hours, then raise the temperature to 132°C for 1.2 hours. During the secondary carbonization process of the present embodiment, the humidity is maintained at 80%;
[0047] In addition, the hot-pressing temperature in step 7) is 135° C., the hot-pressing pressure is 1.2 MPa, and the hot-pressing time is 22 minutes.
PUM
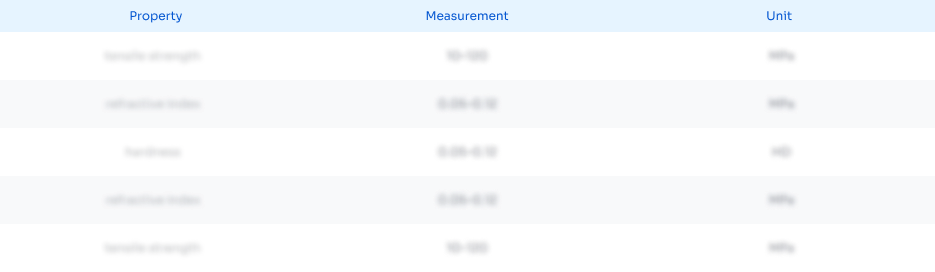
Abstract
Description
Claims
Application Information

- R&D Engineer
- R&D Manager
- IP Professional
- Industry Leading Data Capabilities
- Powerful AI technology
- Patent DNA Extraction
Browse by: Latest US Patents, China's latest patents, Technical Efficacy Thesaurus, Application Domain, Technology Topic, Popular Technical Reports.
© 2024 PatSnap. All rights reserved.Legal|Privacy policy|Modern Slavery Act Transparency Statement|Sitemap|About US| Contact US: help@patsnap.com