Quenching method of major-diameter thick-wall pressure gas cylinder
A large-diameter, gas cylinder technology, applied in the field of heat treatment, can solve the problems of bottle body deformation, low martensite transformation, complex heat treatment process, etc., to achieve the effect of achieving hardness and reducing thermal stress
- Summary
- Abstract
- Description
- Claims
- Application Information
AI Technical Summary
Problems solved by technology
Method used
Image
Examples
Embodiment Construction
[0017] The following examples illustrate the invention.
[0018] Embodiment The gas cylinder has a length of 6000 mm, a wall thickness of 38 mm, an outer diameter of 914 mm, an outer diameter of the mouth of the bottle of 270 mm, and a material of 30CrMo steel. The gas cylinder is heated to 900°C from the heating furnace, and after 45 minutes of heat preservation, it is hoisted by the crane to the roller table of the quenching stand, the inner spray nozzle extends into the inside of the gas cylinder, the rotating wheel starts to rotate, and the gas cylinder starts to spray intermittently on the inner surface and the outer surface. Continuous water spray quenching to ensure that the inner chamber of the gas cylinder can fully release the pressure during the spraying process and keep the internal pressure stable. The specific method is as follows:
[0019] Establish the mathematical model of the gas cylinder quenching process and the grid model of the gas cylinder (the grid mod...
PUM
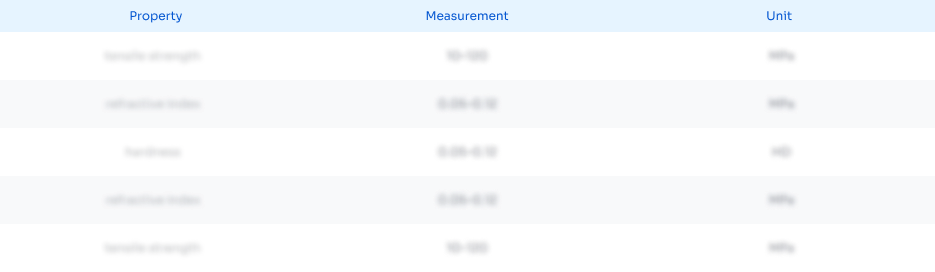
Abstract
Description
Claims
Application Information

- R&D Engineer
- R&D Manager
- IP Professional
- Industry Leading Data Capabilities
- Powerful AI technology
- Patent DNA Extraction
Browse by: Latest US Patents, China's latest patents, Technical Efficacy Thesaurus, Application Domain, Technology Topic, Popular Technical Reports.
© 2024 PatSnap. All rights reserved.Legal|Privacy policy|Modern Slavery Act Transparency Statement|Sitemap|About US| Contact US: help@patsnap.com