Clean production method for hydrofluoroester
A clean production and hydrofluoroether technology, applied in the field of hydrofluoroether production, to achieve the effects of saving production costs, high reaction yield, and avoiding separation
- Summary
- Abstract
- Description
- Claims
- Application Information
AI Technical Summary
Problems solved by technology
Method used
Examples
Embodiment 1
[0028] (1) Add 4610g of trifluoroethanol into a 5L four-necked flask, protect it with nitrogen, and stir mechanically (rotating speed: 500r / min). Add the treated sodium metal into the flask, add sodium metal in 10 batches, and add 23g each time. Wait until the sodium metal has completely disappeared before adding the next batch. The reaction temperature is 60-70°C, and the sodium metal is consumed after 23 hours of reaction to obtain a sodium trifluoroethoxide solution. By detecting the concentration of the solution is about 25%;
[0029] (2) Vacuumize the 10L autoclave, replace it with monomer once, and then evacuate to -0.1MPa, add 2Kg trifluoroethanol, 4Kg sodium trifluoroethoxide solution, then add monomer to 0.4MPa, stir and heat up to 105°C Around this time, start adding tetrafluoroethylene in stages until the pressure of the storage tank is 0.90MPa, while controlling the temperature of the kettle at about 105°C. When the pressure in the kettle drops to 0.7MPa, add tet...
Embodiment 2
[0031] Vacuum the 10L autoclave, replace it once with tetrafluoroethylene, and then evacuate to -0.1MPa, add 2Kg trifluoroethanol, 3Kg sodium trifluoroethoxide solution with a concentration of 25%, then add tetrafluoroethylene to 0.4MPa, and stir Raise the temperature to about 105°C, and start adding tetrafluoroethylene in stages until the pressure of the storage tank is 0.90MPa, while controlling the temperature of the kettle at about 105°C. When the pressure in the kettle drops to 0.7MPa, add tetrafluoroethylene to the tank pressure again, and continue for 2 hours, then start to add tetrafluoroethylene continuously, continue to react for 5 hours, cool down, discharge, weigh, and add tetrafluoroethylene 3.6 Kg. Put the released material into the rectification kettle for rectification, and collect the material with a top temperature of 55-56°C as the hydrofluoroether product. The product purity is 99.6%, and the product yield is 78%.
Embodiment 3
[0033] Vacuum the 10L autoclave, replace it once with tetrafluoroethylene, and then evacuate to -0.1MPa, add 2Kg trifluoroethanol, 5.2Kg sodium trifluoroethoxide solution with a concentration of 25%, and then add tetrafluoroethylene to 0.4MPa, Stir and heat up to about 105°C, start adding tetrafluoroethylene in portions until the pressure of the storage tank is 0.90MPa, while controlling the temperature of the kettle at about 105°C. When the pressure in the kettle drops to 0.7MPa, add tetrafluoroethylene to the tank pressure again, and continue for 2 hours, then start to add tetrafluoroethylene continuously, continue to react for 5 hours, cool down, discharge, weigh, and add tetrafluoroethylene 5.15 Kg. Put the released material into the rectification kettle for rectification, and collect the material with a top temperature of 55-56°C as the hydrofluoroether product. The product purity is 99.4%, and the product yield is 80.2%.
PUM
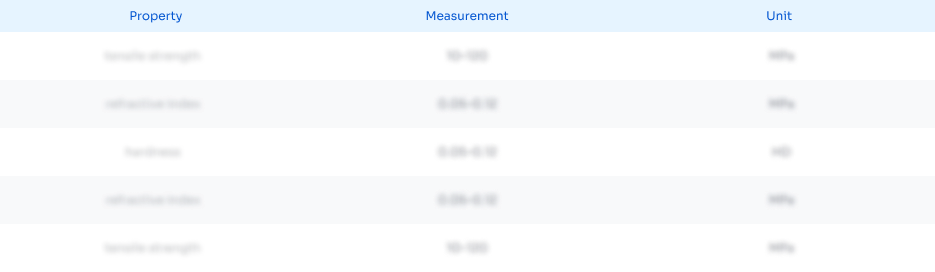
Abstract
Description
Claims
Application Information

- R&D
- Intellectual Property
- Life Sciences
- Materials
- Tech Scout
- Unparalleled Data Quality
- Higher Quality Content
- 60% Fewer Hallucinations
Browse by: Latest US Patents, China's latest patents, Technical Efficacy Thesaurus, Application Domain, Technology Topic, Popular Technical Reports.
© 2025 PatSnap. All rights reserved.Legal|Privacy policy|Modern Slavery Act Transparency Statement|Sitemap|About US| Contact US: help@patsnap.com