Method for manufacturing photoelectric composite medium-voltage drum cable
A process method and photoelectric composite technology, applied in the direction of cable/conductor manufacturing, circuit, electrical components, etc., can solve the problems of difficult control of conductive core and optical unit cabling, difficulty in guaranteeing optical fiber performance, long time, etc., to improve various Item performance and the effect of service life
- Summary
- Abstract
- Description
- Claims
- Application Information
AI Technical Summary
Problems solved by technology
Method used
Image
Examples
Embodiment
[0060] Example: see figure 1 As shown, a photoelectric composite medium-voltage reel cable with a rated voltage of 3.6 / 6kV-12 / 20kV, including three power cores 1 and two ground cores 2 twisted together to form a cable core 10, and an optical unit 3 , the special neoprene inner sheath 5 coated on the outside of the cable core 10, the reinforcement layer 6 braided on the outside of the special neoprene inner sheath 5 and embedded in it, the special neoprene coated on the outside of the reinforcement layer 6 The outer sheath 7 and the reinforcement layer 6 are formed by braiding high-strength polyester filaments. In the cable core 10, three power cores 1 are closely arranged along the circumferential direction, and the central gap between the three power cores 1 is filled with The semi-conductive filler 4, the semi-conductive filler 4 is made of semi-conductive rubber, the two ground wire cores 2 and a light unit 3 are scattered and arranged between the outer sides of two adjace...
PUM
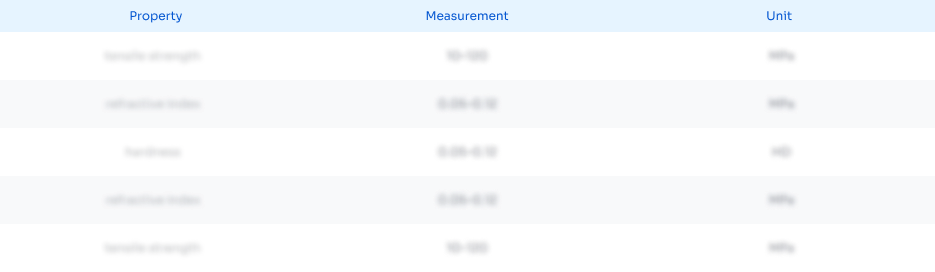
Abstract
Description
Claims
Application Information

- R&D
- Intellectual Property
- Life Sciences
- Materials
- Tech Scout
- Unparalleled Data Quality
- Higher Quality Content
- 60% Fewer Hallucinations
Browse by: Latest US Patents, China's latest patents, Technical Efficacy Thesaurus, Application Domain, Technology Topic, Popular Technical Reports.
© 2025 PatSnap. All rights reserved.Legal|Privacy policy|Modern Slavery Act Transparency Statement|Sitemap|About US| Contact US: help@patsnap.com