Method for recovering mercury from mercury-contained tailings in form of selenide
A technology for selenide and tailings, which is applied in the field of mercury recovery, can solve problems such as complex components, and achieve the effects of simple operation, fast reaction speed, and reduction of pollution hazards.
- Summary
- Abstract
- Description
- Claims
- Application Information
AI Technical Summary
Problems solved by technology
Method used
Examples
Embodiment 1
[0025] Take 1kg of mercury-containing tailings, add 3L of sodium thiosulfate solution with a concentration of 20g / L, stir and leaching at 50°C for 0.5h, and obtain leaching tailings, leaching liquid and washing liquid after liquid-solid separation; The leaching rate of mobile mercury in the medium is 99%;
[0026] Store the separated leaching tailings; combine the leaching solution and washing solution to obtain 4L of a solution containing 700mg of mercury, and add 0.42g of sodium selenide to the solution. After 5 minutes of reaction, add 1g / L 0.08 L of polyacrylamide slurry was subjected to liquid-solid separation to obtain decomposed liquid and mercury selenide precipitate, which was a recovered product, and 99.98% of the mercury in the solution was converted into mercury selenide precipitate.
Embodiment 2
[0028] Take 1 kg of mercury-containing tailings, add a mixed solution of sodium thiosulfate with a concentration of 8 g / L and ammonium thiosulfate with a concentration of 6 g / L, and add 6 L; stir and leaching at 35 ° C for 2 hours, and obtain after liquid-solid separation Leach tailings, leaching solution and washing solution; sampling analysis shows that the leaching rate of migratable mercury in leaching tailings is 99%;
[0029] Store the separated leaching tailings; combine the leaching solution and washing solution to obtain 7L of a solution containing soluble mercury complexes, which contains 700mg of mercury, add 0.54g of sodium selenide to the solution and react for 10min, then add 2g / L poly 0.09L of acrylamide slurry is subjected to liquid-solid separation to obtain decomposition liquid and mercury selenide precipitate, which is the recovered product, and 99.99% of the mercury in the solution is converted into mercury selenide precipitate;
[0030] The decomposition s...
Embodiment 3
[0032] Take 1kg of mercury-containing tailings, add 10L of sodium thiosulfate solution with a concentration of 8g / L, stir and leaching at 20°C for 3h, and obtain leaching tailings, leaching liquid and washing liquid after liquid-solid separation; sampling analysis, leaching tailings The leaching rate of mobile mercury is 99%;
[0033] Store the separated leaching tailings; combine the leaching solution and washing solution to obtain 11L of a solution containing soluble mercury complexes, which contains 700mg of mercury, add 0.70g of sodium selenide to the solution, react for 7min, add 1.5g / L 0.22 L of polyacrylamide slurry was subjected to liquid-solid separation to obtain decomposed liquid and mercury selenide precipitate, which was a recovered product, and 99.99% of the mercury in the solution was converted into mercury selenide precipitate.
PUM
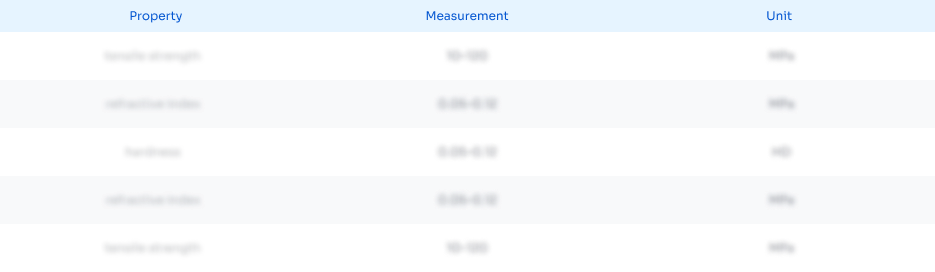
Abstract
Description
Claims
Application Information

- R&D
- Intellectual Property
- Life Sciences
- Materials
- Tech Scout
- Unparalleled Data Quality
- Higher Quality Content
- 60% Fewer Hallucinations
Browse by: Latest US Patents, China's latest patents, Technical Efficacy Thesaurus, Application Domain, Technology Topic, Popular Technical Reports.
© 2025 PatSnap. All rights reserved.Legal|Privacy policy|Modern Slavery Act Transparency Statement|Sitemap|About US| Contact US: help@patsnap.com