High-antimony bismuth-containing material treatment technology
A processing technology and material technology, applied in the processing technology field of high antimony and bismuth-containing materials, can solve the problems of high time consumption, high cost and high energy consumption
- Summary
- Abstract
- Description
- Claims
- Application Information
AI Technical Summary
Problems solved by technology
Method used
Image
Examples
Embodiment 1
[0024] (1) Reverberatory furnace reduction smelting process
[0025] The high-antimony bismuth-containing material mainly contains Sb and a small amount of Cu impurity elements. The high-antimony bismuth-containing material and bismuth sulfide are mixed evenly, and then added to the reverberatory furnace together with lime, soda ash, iron filings and coke powder for reduction smelting. 500°C and smelting time of 2 hours. After the smelting is over, remove the slag to obtain thick bismuth, thin slag and sticky slag for later use; wherein, the amount of bismuth sulfide added is 20% by mass of the high-antimony bismuth-containing material, and the lime The addition accounts for 8% of the mass percentage of high antimony and bismuth-containing materials, the addition of said soda ash accounts for 20% of the mass percentage of high antimony and bismuth-containing materials, and the addition of said iron filings accounts for 5% of the mass percentage of high antimony and bismuth-cont...
Embodiment 2
[0039] (1) Reverberatory furnace reduction smelting process
[0040] The high-antimony bismuth-containing material mainly contains Sb and a small amount of Cu impurity elements. The high-antimony bismuth-containing material and bismuth sulfide are mixed evenly, and then added to the reverberatory furnace together with lime, soda ash, iron filings and coke powder for reduction smelting. 600°C, smelting time of 8 hours, after the smelting, remove the slag, obtain thick bismuth, thin slag and sticky slag, and set aside; wherein, the added amount of the bismuth sulfide accounts for 15% of the mass percentage of the high-antimony bismuth-containing material, and the lime Addition accounted for high antimony bismuth material mass percentage is 5%, said soda ash addition accounts for high antimony bismuth material mass percentage is 10%, said iron filings addition accounts for high antimony bismuth material mass percentage is 2.5%; Melting After finishing, the slag is removed to obta...
Embodiment 3
[0054] (1) Reverberatory furnace reduction smelting process
[0055] The high-antimony bismuth-containing material mainly contains Sb and a small amount of Cu impurity elements. The high-antimony bismuth-containing material and bismuth sulfide are mixed evenly, and then added to the reverberatory furnace together with lime, soda ash, iron filings and coke powder for reduction smelting. 700°C and smelting time of 12 hours. After the smelting is over, remove the slag to obtain thick bismuth, thin slag and sticky slag for later use; wherein, the amount of bismuth sulfide added is 10% by mass of the high-antimony bismuth-containing material, and the lime The addition amount accounts for 3% of the mass percentage of high antimony and bismuth-containing material, the addition of said soda ash accounts for 5% of the mass percentage of high antimony and bismuth-containing material, and the addition of said iron filings accounts for 1% of the mass percentage of high antimony and bismuth...
PUM
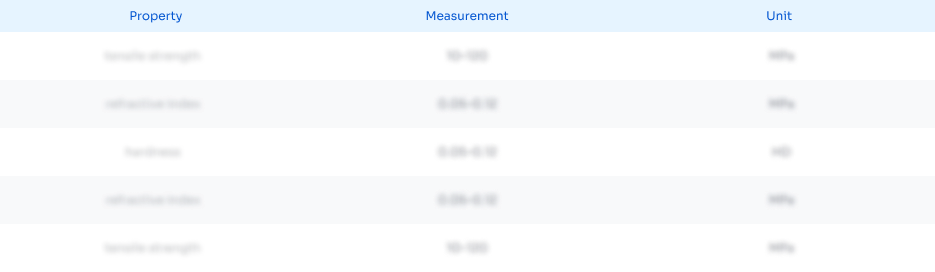
Abstract
Description
Claims
Application Information

- Generate Ideas
- Intellectual Property
- Life Sciences
- Materials
- Tech Scout
- Unparalleled Data Quality
- Higher Quality Content
- 60% Fewer Hallucinations
Browse by: Latest US Patents, China's latest patents, Technical Efficacy Thesaurus, Application Domain, Technology Topic, Popular Technical Reports.
© 2025 PatSnap. All rights reserved.Legal|Privacy policy|Modern Slavery Act Transparency Statement|Sitemap|About US| Contact US: help@patsnap.com