Toughened high density polyethylene 3D printing moulding material and preparation method thereof
A high-density polyethylene and 3D printing technology, applied in the field of 3D printing molding materials, can solve the problems of difficult handling, complicated operation, and complicated FDM of nanofiber composite lines, and achieve the effect of low production cost and simple production process
- Summary
- Abstract
- Description
- Claims
- Application Information
AI Technical Summary
Problems solved by technology
Method used
Image
Examples
Embodiment 1
[0048] A toughened high-density polyethylene 3D printing molding material, the formula of which is as follows:
[0049]
[0050] The master batch is added by adding 100 parts of ethylene-propylene elastomer, 1000 parts of xylene diluent, 0.25 parts of BPO and 4.0 parts of DMSO into a reactor equipped with a stirrer, a reflux condenser, and a thermometer, stirring and heating to 125 ° C, After reacting for 3 hours, a toughening masterbatch was prepared. Mix 68 parts of 2200J high-density polyethylene, 10 parts of carbon nanotubes and 0.2 parts of antioxidant tris[2,4-di-tert-butylphenyl] phosphite with 32 parts of toughening masterbatch, in Extrude and granulate on a twin-screw extruder to prepare a blend. The temperature from the feeding section to the nozzle die is 130, 135, 155, 165, 185, 180°C; the main screw speed is 90r / min.
Embodiment 2
[0052] A toughened high-density polyethylene 3D printing molding material, the formula of which is as follows:
[0053]
[0054] Add 80 parts of ethylene-propylene elastomer, 20 parts of styrene-butadiene elastomer, 1000 parts of xylene solvent, 0.25 parts of BPO, and 4.0 parts of DMSO into the reactor equipped with agitator, reflux condenser, and thermometer, stir and heat up to 125°C , and reacted for 3 hours to prepare a toughening masterbatch. Mix 64 parts of 2200J high-density polyethylene, 20 parts of carbon nanotubes and 0.2 parts of tris[2.4-di-tert-butylphenyl] phosphite with 36 parts of toughening masterbatch, and extrude in twin-screw Extrude and granulate on the machine to prepare the blend. The temperature from the feeding section to the nozzle die is 130, 135, 155, 165, 185, 180°C; the main screw speed is 90r / min.
Embodiment 3
[0056] A toughened high-density polyethylene 3D printing molding material, the formula of which is as follows:
[0057]
[0058] Add 60 parts of ethylene-propylene elastomer, 40 parts of styrene-butadiene elastomer, 1000 parts of xylene solvent, 0.25 parts of BPO and 4.0 parts of DMSO into the reactor equipped with a stirrer, reflux condenser and thermometer, stir and heat up to 125°C , reacted for 3 hours to prepare the toughening masterbatch under the formula. 60 parts of 2200J high-density polyethylene, 15 parts of carbon nanotubes and 0.1 parts of antioxidant tris[2.4-di-tert-butylphenyl] phosphite were mixed with 40 parts of toughening masterbatch in a twin-screw Extrude and granulate on an extruder to prepare a blend. The temperature from the feeding section to the nozzle die is 130, 135, 155, 165, 185, 180°C; the main screw speed is 90r / min. Example 4
PUM
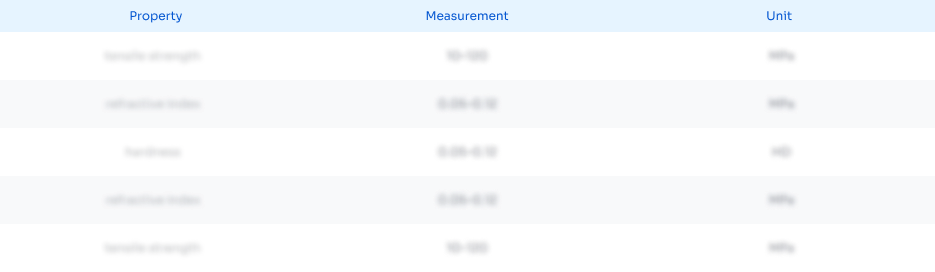
Abstract
Description
Claims
Application Information

- R&D
- Intellectual Property
- Life Sciences
- Materials
- Tech Scout
- Unparalleled Data Quality
- Higher Quality Content
- 60% Fewer Hallucinations
Browse by: Latest US Patents, China's latest patents, Technical Efficacy Thesaurus, Application Domain, Technology Topic, Popular Technical Reports.
© 2025 PatSnap. All rights reserved.Legal|Privacy policy|Modern Slavery Act Transparency Statement|Sitemap|About US| Contact US: help@patsnap.com