Method for preparing heavy metal adsorbent by utilizing caustic dross
An adsorbent and heavy metal technology, which is applied in the field of heavy metal adsorbent preparation by using alkali slag, can solve the problems of difficult large-scale industrial application, secondary pollution needs to be studied, and high preparation cost, so as to improve adsorption capacity, reduce application cost, and widely Effect of the pH range of application
- Summary
- Abstract
- Description
- Claims
- Application Information
AI Technical Summary
Problems solved by technology
Method used
Examples
Embodiment 1
[0039] 1) Pretreatment of alkali slag: After the alkali slag is crushed, it is washed with water, dried at 100°C, and ground until it passes through a 100-mesh sieve for later use;
[0040] 2) Synthesis of powdered adsorbent: 5.0 g of pretreated alkali slag was added to 200 mL of 1 mol / L commercial phosphoric acid solution, 15.0 g of sodium ethylenediaminetetraacetic acid (EDTA) was added, and fully stirred at 40°C. After the stirring is completed, filter the filtrate, adjust its pH to 9.0 with lye, and then transfer it to a reaction kettle with a polytetrafluoroethylene inner inch. Control the reaction temperature at 150°C and the reaction time for 14 hours. After the reaction, centrifuge to obtain a solid, and wash it with water. After drying, the powdered adsorbent is obtained;
[0041] 3) Preparation of heavy metal adsorbent: mix the powdered adsorbent prepared in 2) with clay and activated sludge according to 65%: 25%: 10%, then granulate, and then calcined at 550°C for 2...
Embodiment 2
[0044] 1) Pretreatment of alkali slag: After the alkali slag is crushed, it is washed with water, dried at 100°C, and ground until it passes through a 100-mesh sieve for later use;
[0045] 2) Synthesis of powdered adsorbent: Take 5.0g of pretreated alkali slag and add it to 200mL of diluted waste etching solution (containing phosphoric acid concentration 1mol / L), add 15.0g of sodium ethylenediaminetetraacetate (EDTA) , fully stirred at 40°C. After the stirring is completed, filter the filtrate, adjust its pH to 9.0 with lye, and then transfer it to a reaction kettle with a polytetrafluoroethylene inner inch. Control the reaction temperature at 150°C and the reaction time for 14 hours. After the reaction, centrifuge to obtain a solid, and wash it with water. After drying, the powdered adsorbent is obtained;
[0046]3) Preparation of heavy metal adsorbent: mix the powdered adsorbent prepared in 2) with clay and activated sludge according to 65%: 25%: 10%, then granulate, and t...
Embodiment 3
[0049] 1) Pretreatment of alkali slag: After the alkali slag is crushed, it is washed with water, dried at 80°C, and ground until it passes through a 200-mesh sieve for later use;
[0050] 2) Synthesis of powdered adsorbent: Take 1.0g of pretreated alkali slag and add it to 100mL of diluted crude phosphoric acid (phosphate root concentration is 0.47mol / L), add 1.7g of ethylene glycol bis(2-amino Ethyl ether) tetraacetic acid (EGTA), fully stirred at 60°C. After the stirring is completed, filter and take the filtrate, adjust its pH to 8.0 with lye, and then transfer it to the reaction kettle in the inner village of polytetrafluoroethylene. After that, the powdered adsorbent is obtained;
[0051] 3) Preparation of heavy metal adsorbent: mix the powdered adsorbent prepared in 2) with cement, clay mixture (1:1), and activated sludge according to 70%: 27%: 3%, then granulate, and then granulate at 600 The heavy metal adsorbent was obtained by calcining at ℃ for 4 hours.
[0052]...
PUM
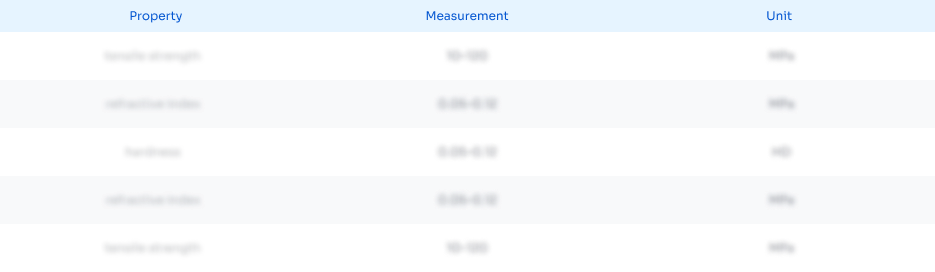
Abstract
Description
Claims
Application Information

- Generate Ideas
- Intellectual Property
- Life Sciences
- Materials
- Tech Scout
- Unparalleled Data Quality
- Higher Quality Content
- 60% Fewer Hallucinations
Browse by: Latest US Patents, China's latest patents, Technical Efficacy Thesaurus, Application Domain, Technology Topic, Popular Technical Reports.
© 2025 PatSnap. All rights reserved.Legal|Privacy policy|Modern Slavery Act Transparency Statement|Sitemap|About US| Contact US: help@patsnap.com