Composite profile and manufacturing method for macromolecular profile in composite profile
A technology of composite profiles and polymers, applied in window/door frames, leaf frames, etc., can solve problems such as large gaps in thermal expansion coefficients, imperfect processing technology, loose lap joints, etc., and achieve low linear expansion coefficients and excellent Good mechanical properties and creep resistance
- Summary
- Abstract
- Description
- Claims
- Application Information
AI Technical Summary
Problems solved by technology
Method used
Image
Examples
Embodiment 1
[0035] A composite profile. The polymer profile and the aluminum profile are compounded by a roller press, wherein the polymer profile is made of components containing the following mass percentages:
[0036] Glass fiber 25%,
[0037] Metal mineral reinforcement 5%,
[0038] Modified polyurethane 70%.
[0039] The modified polyurethane is synthesized from isocyanate and polyol, and its mass ratio is 1.08:1.
[0040] A method for preparing polymer profiles in composite profiles includes the following steps:
[0041] Step 1. Yarn feeding: the glass fiber roving yarn group is installed on the creel, and the unwound yarn bundle enters the injection chamber after passing through the guide roller, the gathering grid and the gathering roller;
[0042] Step 2. Dipping: After measuring the isocyanate, polyol and metal mineral reinforcement through the metering pump, put them in a static mixer for mixing, and then pump them into the injection chamber to soak the glass fiber that has entered the inj...
Embodiment 2
[0051] A composite profile. The polymer profile and the aluminum profile are compounded by a roller press, wherein the polymer profile is made of components containing the following mass percentages:
[0052] Glass fiber 25%,
[0053] Metal mineral reinforcement 2%,
[0054] Modified polyurethane 73%.
[0055] The modified polyurethane is synthesized from isocyanate and polyol, and its mass ratio is 1.08:1.
[0056] A method for preparing polymer profiles in composite profiles includes the following steps:
[0057] Step 1. Yarn feeding: the glass fiber roving yarn group is installed on the creel, and the unwound yarn bundle enters the injection chamber after passing through the guide roller, the gathering grid and the gathering roller;
[0058] Step 2. Dipping: After measuring the isocyanate, polyol and metal mineral reinforcement by the metering pump, put them in a static mixer for mixing, and then pump them into the injection chamber to soak the glass fiber that has entered the injectio...
Embodiment 3
[0067] A composite profile. The polymer profile and the aluminum profile are compounded by a roller press, wherein the polymer profile is made of components containing the following mass percentages:
[0068] Glass fiber 25%,
[0069] Metal mineral reinforcement 8%,
[0070] Modified polyurethane 67%.
[0071] The modified polyurethane is synthesized from isocyanate and polyol, and its mass ratio is 1.08:1.
[0072] A method for preparing polymer profiles in composite profiles includes the following steps:
[0073] Step 1. Yarn feeding: the glass fiber roving yarn group is installed on the creel, and the unwound yarn bundle enters the injection chamber after passing through the guide roller, the gathering grid and the gathering roller;
[0074] Step 2. Dipping: After measuring the isocyanate, polyol and metal mineral reinforcement by the metering pump, put them in a static mixer for mixing, and then pump them into the injection chamber to soak the glass fiber that has entered the injectio...
PUM
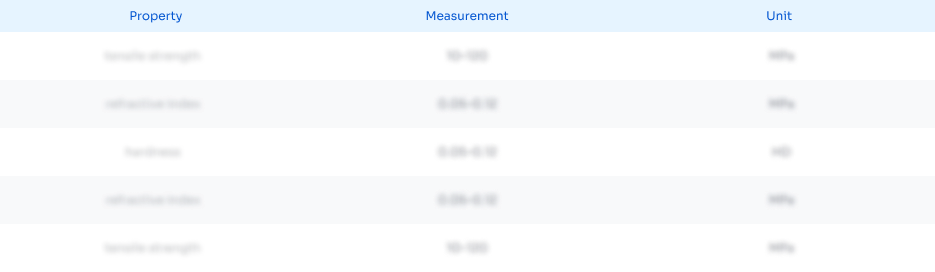
Abstract
Description
Claims
Application Information

- Generate Ideas
- Intellectual Property
- Life Sciences
- Materials
- Tech Scout
- Unparalleled Data Quality
- Higher Quality Content
- 60% Fewer Hallucinations
Browse by: Latest US Patents, China's latest patents, Technical Efficacy Thesaurus, Application Domain, Technology Topic, Popular Technical Reports.
© 2025 PatSnap. All rights reserved.Legal|Privacy policy|Modern Slavery Act Transparency Statement|Sitemap|About US| Contact US: help@patsnap.com