Method for preparing composite photocatalysis bleaching system and textile bleaching technology
A technology of composite photocatalysis and system, which is applied in the field of composite photocatalysis system and bleaching process, can solve the problems such as environmental pollution cannot be effectively solved, and achieve the effects of short processing time, small loss of strength and high whiteness
- Summary
- Abstract
- Description
- Claims
- Application Information
AI Technical Summary
Problems solved by technology
Method used
Image
Examples
Embodiment 1
[0029] A preparation method of a composite photocatalytic bleaching system, comprising the following steps:
[0030] (1), adding 12 g of hydrogen peroxide with a mass concentration of 30% in 1 L of water, adjusting the pH value to 10.5 with sodium bicarbonate, adding 1 g of a stabilizer, to obtain a hydrogen peroxide bleaching system;
[0031] (2) Add 20 g of titanium dioxide, 5 g of sodium dodecylbenzenesulfonate and 1 g of sodium hexametaphosphate into 1 L of water, adjust the pH to 9, and ultrasonically disperse for 30 minutes to prepare a titanium dioxide dispersion system.
[0032] The preparation method of the stabilizer is as follows: adding phytic acid aqueous solution into a high-pressure reaction kettle, filling ammonia water from the bottom of the reaction kettle under stirring conditions, pressurizing to 2MPa, and gradually raising the temperature to 40°C at the same time, stirring for 20min, cooling to room temperature, reducing Press to obtain ammonium phytate. ...
Embodiment 2
[0038] A preparation method of a composite photocatalytic bleaching system, comprising the following steps:
[0039] (1), adding 5 g of hydrogen peroxide with a mass concentration of 30% in 1 L of water, adjusting the pH value to 10.7 with sodium bicarbonate, adding 2 g of a stabilizer, to obtain a hydrogen peroxide bleaching system;
[0040] (2) Add 15 g of titanium dioxide, 3 g of sodium dodecylbenzenesulfonate and 1 g of sodium hexametaphosphate into 1 L of water, adjust the pH to 9, and ultrasonically disperse for 20 minutes to prepare a titanium dioxide dispersion system.
[0041] Add phytic acid aqueous solution into the high-pressure reaction kettle, and fill it with ammonia water from the bottom of the reaction kettle under the stirring condition of rotating speed of 300 rpm, pressurize to 3MPa, and gradually raise the temperature to 50°C at the same time, stirring at a rotating speed of 300 rpm for 30 minutes, Cool to room temperature and reduce pressure to obtain amm...
Embodiment 3
[0047] A preparation method of a composite photocatalytic bleaching system, comprising the following steps:
[0048] (1), adding 5 g of hydrogen peroxide with a mass concentration of 30% in 1 L of water, adjusting the pH value to 10.8 with sodium bicarbonate, adding 3 g of a stabilizer, to obtain a hydrogen peroxide bleaching system;
[0049] (2) Add 25g of titanium dioxide, 3g of sodium dodecylbenzenesulfonate and 1g of sodium hexametaphosphate into 1L of water, adjust the pH to 9, and ultrasonically disperse for 40 minutes to prepare a titanium dioxide dispersion system.
[0050] Add phytic acid aqueous solution into the high-pressure reaction kettle, and fill it with ammonia water from the bottom of the reaction kettle under the stirring condition of rotating speed of 300 rpm, pressurize to 5MPa, and gradually raise the temperature to 50°C at the same time, stirring at a rotating speed of 300 rpm for 30 minutes, Cool to room temperature and reduce pressure to obtain ammoniu...
PUM
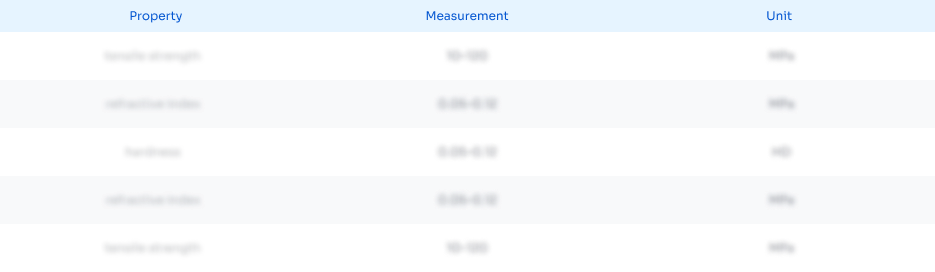
Abstract
Description
Claims
Application Information

- Generate Ideas
- Intellectual Property
- Life Sciences
- Materials
- Tech Scout
- Unparalleled Data Quality
- Higher Quality Content
- 60% Fewer Hallucinations
Browse by: Latest US Patents, China's latest patents, Technical Efficacy Thesaurus, Application Domain, Technology Topic, Popular Technical Reports.
© 2025 PatSnap. All rights reserved.Legal|Privacy policy|Modern Slavery Act Transparency Statement|Sitemap|About US| Contact US: help@patsnap.com