Method for predicting milling force of five-axis numerical control side milling
A technology of milling force and side milling, applied in program control, computer control, general control system, etc., can solve problems such as low precision and efficiency
- Summary
- Abstract
- Description
- Claims
- Application Information
AI Technical Summary
Problems solved by technology
Method used
Image
Examples
Embodiment Construction
[0054] The following is a detailed description of the embodiments of the present invention: this embodiment is implemented on the premise of the technical solution of the present invention, and provides detailed implementation methods and specific operation processes. It should be noted that those skilled in the art can make several modifications and improvements without departing from the concept of the present invention, and these all belong to the protection scope of the present invention.
[0055] This embodiment provides a milling force prediction method for five-axis CNC side milling, such as figure 1 shown.
[0056] This embodiment specifically includes the following steps:
[0057] Step 1, read in data: read in the blank model file, tool path file, and tool geometry parameters, and interpolate the discrete tool positions to obtain the tool axis surface and store it;
[0058] Preferably, the blank model file is a known CAD model of the blank to be processed, and the t...
PUM
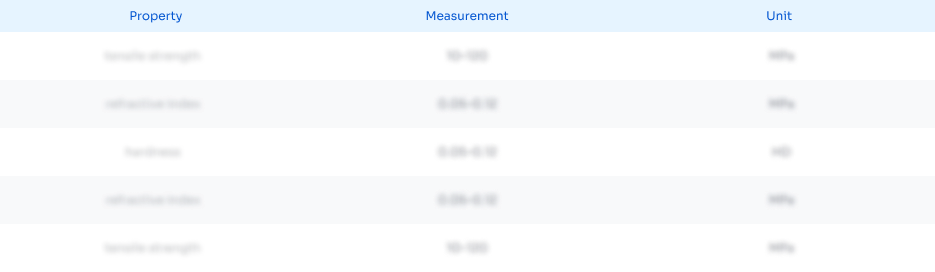
Abstract
Description
Claims
Application Information

- R&D
- Intellectual Property
- Life Sciences
- Materials
- Tech Scout
- Unparalleled Data Quality
- Higher Quality Content
- 60% Fewer Hallucinations
Browse by: Latest US Patents, China's latest patents, Technical Efficacy Thesaurus, Application Domain, Technology Topic, Popular Technical Reports.
© 2025 PatSnap. All rights reserved.Legal|Privacy policy|Modern Slavery Act Transparency Statement|Sitemap|About US| Contact US: help@patsnap.com