High-temperature-resistant mirror silver resin and preparation method thereof
A technology of mirror-surface silver resin and high temperature resistance, which is applied in the direction of coating, etc., can solve the problems of unenvironmental protection of raw materials or synthesis process, high cost of synthesis process, poor solvent resistance of resin, etc., achieve broad-spectrum adhesion, and the synthesis process is green and environmentally friendly , good solvent resistance
- Summary
- Abstract
- Description
- Claims
- Application Information
AI Technical Summary
Problems solved by technology
Method used
Image
Examples
preparation example Construction
[0019] The preparation method of the above-mentioned high temperature-resistant mirror silver resin comprises the steps of: adding cellulose acetate butyrate in the first component into a solvent to dissolve, heating while stirring, raising the temperature to 70-95° C., and protecting with nitrogen gas; Mix all the materials in the second component, add dropwise to the first component in 3.5-4.5 hours, keep warm for 1-1.5 hours, and raise the temperature to 85-110°C; add the third component, keep warm for 2-2.5 hours, and finally Cool and filter.
[0020] Preferably, the cellulose acetate butyrate is at least one of CAB381-0.1, CAB381-0.5, CAB381-2, and CAB381-20.
[0021] Described initiator is oil-soluble peroxide or azo compound; Preferably, described oil-soluble peroxide is benzoyl peroxide, tert-butyl peroxybenzoate, dicumyl peroxide, peroxide At least one of di-tert-butyl oxide and methyl ethyl ketone peroxide; the azo compound is at least one of azobisisobutyronitrile ...
Embodiment 1
[0025] Nitrogen was blown in the four-neck flask, 200 parts of butyl acetate and 50 parts of xylene were added, stirred while heating, then 50 parts of CAB381-2 was added to dissolve, and the temperature was raised to 80°C. Start dropping the following mixture, 40 parts of methyl methacrylate\20 parts of butyl acetate\10 parts of hydroxyethyl methacrylate\10 parts of hydroxypropyl methacrylate\40 parts of epoxy methacrylate\ 1 part of initiator, azobisisobutyronitrile, was dripped in 4 hours, and kept warm for 1 hour after dripping. Add 1 part of azobisisobutyronitrile\20 parts of butyl acetate, keep warm for 2 hours, and filter.
Embodiment 2
[0027] Nitrogen was blown in the four-neck flask, 300 parts of ethylene glycol methyl ether acetate was added, stirred while heating, then 50 parts of CAB381-20 was added to dissolve, and the temperature was raised to 85-90°C. Start dropping the following mixture, 50 parts of methyl methacrylate\20 parts of butyl acetate\10 parts of hydroxyethyl methacrylate\10 parts of hydroxypropyl methacrylate\30 parts of epoxy methacrylate\ Mix 10 parts of isobornyl methacrylate\1.5 parts of benzoyl peroxide, drop it in 4 hours, and keep it warm for 1 hour after the drop. Add 1 part of benzoyl peroxide\20 parts of butyl acetate, keep warm for 2 hours, and filter.
PUM
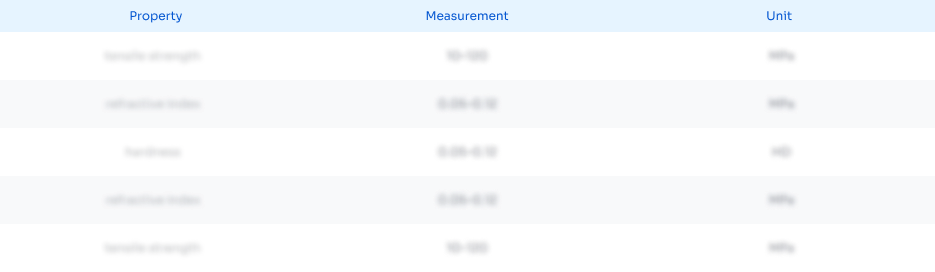
Abstract
Description
Claims
Application Information

- Generate Ideas
- Intellectual Property
- Life Sciences
- Materials
- Tech Scout
- Unparalleled Data Quality
- Higher Quality Content
- 60% Fewer Hallucinations
Browse by: Latest US Patents, China's latest patents, Technical Efficacy Thesaurus, Application Domain, Technology Topic, Popular Technical Reports.
© 2025 PatSnap. All rights reserved.Legal|Privacy policy|Modern Slavery Act Transparency Statement|Sitemap|About US| Contact US: help@patsnap.com