Ester solvent environment-friendly thermoplastic acrylic coating and preparation method thereof
A thermoplastic acrylic, ester solvent technology, applied in the direction of coating, etc.
- Summary
- Abstract
- Description
- Claims
- Application Information
AI Technical Summary
Problems solved by technology
Method used
Image
Examples
Embodiment 1
[0105] First, 10 kg of tert-butyl acetate, 20 kg of sec-butyl acetate, 20 kg of dibasic acid ester, and 20 kg of dimethyl carbonate are uniformly mixed in proportion through a high-speed disperser and configured as an "ester solvent". The speed is: 650 ~1450 rpm, the time is 5 minutes; then "ester solvent", high solid content (solid content ≥ 60%), 90 kg of aromatic-free thermoplastic acrylic resin, 25 kg of rutile titanium dioxide, silica filler 5 kg, 5 kg of additives (one or more of wetting dispersant, defoamer, thickener, antifouling and antifungal agent), uniformly mixed by a high-speed disperser for 10 minutes; the mixture is sand-milled Machine grinding twice, each time is 0.5 hours; finally, pour 4 kg of 2-ethylhexyl acetate solvent into it, after uniform stirring, grind for 1 hour again, and the finished product can be obtained when the fineness reaches below 25 μm.
Embodiment 2
[0107] Firstly, 15 kg of tert-butyl acetate, 25 kg of sec-butyl acetate, 25 kg of dibasic acid ester, and 25 kg of dimethyl carbonate are uniformly mixed in proportion by a high-speed disperser to form an "ester solvent". The speed is: 650 ~1450 rpm, the time is 5 minutes; then add "ester solvent", high solid content (solid content ≥ 60%), 120 kg of aromatic-free thermoplastic acrylic resin, 35 kg of rutile titanium dioxide, silica filler 8 kg, 6 kg of additives (one or more of wetting dispersant, defoamer, thickener, antifouling and antifungal agent) are uniformly mixed by a high-speed disperser for 10 minutes; the mixture is passed through a sand mill Grind twice, each time for 1 hour; finally, pour 6 kg of 2-ethylhexyl acetate solvent into it, stir evenly, and grind for 1 hour again, and the finished product can be obtained when the fineness reaches below 25 μm.
Embodiment 3
[0109] Firstly, 20 kg of tert-butyl acetate, 30 kg of sec-butyl acetate, 30 kg of dibasic acid ester, and 30 kg of dimethyl carbonate are uniformly mixed in proportion by a high-speed disperser and configured as an "ester solvent". The speed is: 650 ~1450 rpm, the time is 5 minutes; then "ester solvent", high solid content (solid content ≥ 60%), 150 kg of aromatic-free thermoplastic acrylic resin, 50 kg of rutile titanium dioxide, silica filler 10 kg, 8 kg of additives (one or more of wetting dispersant, defoamer, thickener, antifouling and antifungal agent) are uniformly mixed by a high-speed disperser for 10 minutes; the mixture is passed through a sand mill Grind twice, each time for 1.5 hours; finally, pour 8 kg of 2-ethylhexyl acetate solvent into it, stir evenly, and grind for 1 hour again, and the finished product can be obtained when the fineness reaches below 25 μm.
[0110]
[0111]
[0112] In the present invention, the thermoplastic acrylic paint produced by su...
PUM
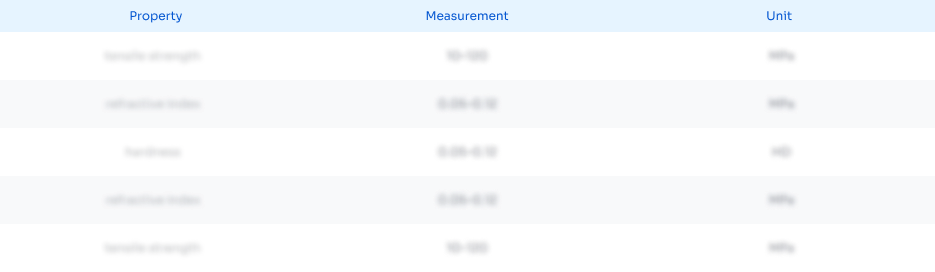
Abstract
Description
Claims
Application Information

- R&D
- Intellectual Property
- Life Sciences
- Materials
- Tech Scout
- Unparalleled Data Quality
- Higher Quality Content
- 60% Fewer Hallucinations
Browse by: Latest US Patents, China's latest patents, Technical Efficacy Thesaurus, Application Domain, Technology Topic, Popular Technical Reports.
© 2025 PatSnap. All rights reserved.Legal|Privacy policy|Modern Slavery Act Transparency Statement|Sitemap|About US| Contact US: help@patsnap.com