Test device and method for measuring residual stress of coating
A technology of residual stress and test equipment, applied in the direction of measuring equipment, measuring force, instruments, etc., can solve problems such as uneven organization and structure
- Summary
- Abstract
- Description
- Claims
- Application Information
AI Technical Summary
Problems solved by technology
Method used
Image
Examples
Embodiment Construction
[0070] Below, the substrate is Ti-6Al-4V (TC4) plate, and the coating is ZrO 2 Taking powder as an example, this method is further described in detail:
[0071] 1. The substrate material is Ti-6Al-4V (TC4) plate, and the plate size is 200mm×15mm×2mm. The powder is ZrO 2 Powder (5~60μm).
[0072] 2. Before spraying, clean the substrate with acetone and roughen it with 10-30 mesh corundum under a pressure of 0.5 MPa, and then clean the surface.
[0073] 3. One end of the specimen is clamped on the clamp.
[0074] 4. Here, the contact displacement sensor is placed on the unclamped end of the sample, and the contact temperature sensor is placed on the clamped end of the sample.
[0075] 5. Through the test circuit, in the computer, collect and record the changes of displacement and temperature data.
[0076] 6. Use a plasma spray gun to carry out plasma spraying on the surface of the sample, and go back and forth 3 times. Record the data.
[0077] 7. By the data obtained, a...
PUM
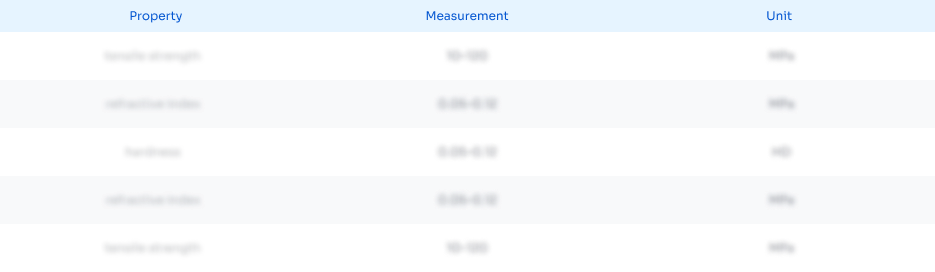
Abstract
Description
Claims
Application Information

- R&D Engineer
- R&D Manager
- IP Professional
- Industry Leading Data Capabilities
- Powerful AI technology
- Patent DNA Extraction
Browse by: Latest US Patents, China's latest patents, Technical Efficacy Thesaurus, Application Domain, Technology Topic, Popular Technical Reports.
© 2024 PatSnap. All rights reserved.Legal|Privacy policy|Modern Slavery Act Transparency Statement|Sitemap|About US| Contact US: help@patsnap.com